IoT in manufacturing is rapidly transforming industrial processes, enabling real-time data collection, predictive maintenance, and enhanced automation. This technology connects machines and devices, creating a smart factory environment where insights drive efficiency and productivity. The interconnected network of sensors, actuators, and data analytics platforms is reshaping the manufacturing landscape, offering unprecedented opportunities for optimization and improvement.
The increasing use of IoT in manufacturing is paving the way for a more agile and responsive production system. From optimizing supply chains to improving safety measures, IoT solutions offer significant advantages for manufacturers. By leveraging the power of data and advanced analytics, businesses can make better decisions, reduce downtime, and enhance overall performance.
Introduction to IoT in Manufacturing
The Internet of Things (IoT) is rapidly transforming manufacturing by connecting physical devices and machines to a digital network. This connectivity enables real-time data collection, analysis, and automation, leading to increased efficiency, productivity, and cost savings. By integrating sensors, actuators, and communication protocols, manufacturers can gain unprecedented insights into their operations, optimize processes, and enhance product quality.IoT in manufacturing leverages data-driven decision-making to optimize resource allocation, improve supply chain management, and enhance safety protocols.
This allows manufacturers to respond more dynamically to changing market demands and customer needs. The core principles involve connecting devices, collecting data, analyzing it, and then acting on the insights derived.
Key Concepts and Principles of IoT in Manufacturing
The foundation of IoT in manufacturing relies on several key concepts. Data collection from various sources, including sensors embedded in machinery and equipment, is crucial for understanding operational parameters. This data, once collected, is processed and analyzed to identify patterns, predict potential issues, and optimize performance. Crucially, this analysis allows for proactive maintenance and minimizes downtime. The ability to communicate and act upon this data in real-time is essential to achieving the full benefits of IoT.
Examples of IoT Transforming Manufacturing Processes, IoT in manufacturing
IoT is already impacting various manufacturing stages, from production to logistics. One example is predictive maintenance, where sensors monitor equipment health in real-time. By identifying patterns indicative of potential failures, manufacturers can schedule maintenance proactively, preventing costly breakdowns. Another example is the optimization of supply chain logistics. IoT sensors can track inventory levels and delivery times, enabling more efficient resource allocation and reducing waste.
Furthermore, quality control is enhanced through automated inspections, where IoT devices can detect defects with higher accuracy and speed. Smart factories are emerging, where these connected devices and systems collaborate seamlessly.
Architecture of an IoT-Enabled Manufacturing System
The architecture of an IoT-enabled manufacturing system typically comprises interconnected components. A simplified diagram depicts the flow of information:
+-----------------+ +-----------------+ +-----------------+ | Sensors |-----| Data Acquisition |-----| Data Processing | +-----------------+ +-----------------+ +-----------------+ | (Machine, | | (Gateway, Cloud) | | (Cloud, | | Equipment, | | (Data Storage) | | Analytics) | | Product) | +-----------------+ +-----------------+ +-----------------+ | | | +-----------------+ | | Control System | | +-----------------+ | | (Automated | | | Decision Making) | | +-----------------+ +-----------------------+ | Actuators | +-----------------------+ (Machines, | Equipment) | | | Feedback Loop
This diagram illustrates the flow of data from sensors, through data acquisition and processing, to control systems and back to the sensors, creating a closed-loop feedback mechanism.
The core components are sensors, data acquisition systems (often cloud-based), data processing units (including algorithms and analytics), and actuators, which respond to the processed data.
Data Collection and Monitoring in Manufacturing
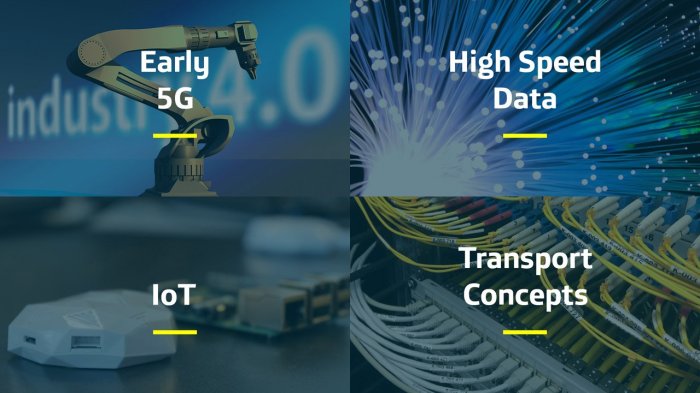
IoT in manufacturing significantly enhances operational efficiency by providing real-time insights into equipment performance and production processes. This data-driven approach allows manufacturers to optimize resource allocation, reduce downtime, and improve product quality. Effective data collection and monitoring are crucial for leveraging the full potential of IoT in the factory.
Real-time monitoring of equipment and processes is vital for identifying potential issues and proactively addressing them before they impact production. Accurate and timely data collection allows manufacturers to make informed decisions and maintain a smooth production flow. This enables a more responsive and adaptable manufacturing environment.
Types of Data Collected
A variety of data points are gathered from IoT devices within manufacturing settings. These include sensor readings, machine performance metrics, and environmental conditions. This rich dataset provides a comprehensive view of the entire manufacturing process.
- Sensor Readings: Temperature, pressure, vibration, and humidity levels are crucial indicators of equipment health and process parameters. These readings can be monitored to detect anomalies and predict potential equipment failures.
- Machine Performance Metrics: Data on production output, cycle times, energy consumption, and machine uptime are collected to optimize efficiency and identify bottlenecks in the production line. This data allows for a detailed analysis of machine performance over time.
- Environmental Conditions: Monitoring factors like ambient temperature, lighting, and air quality within the factory environment helps maintain optimal working conditions and identify potential issues related to environmental factors affecting production or employee comfort.
Real-Time Monitoring Methods
Various methods enable real-time monitoring of manufacturing equipment and processes. These methods ensure immediate responses to potential issues.
- Industrial Ethernet: This network infrastructure facilitates high-speed data transfer, allowing for near real-time monitoring and control of manufacturing processes. The high bandwidth enables efficient data transmission to control systems and displays.
- Wireless Sensor Networks (WSNs): These networks allow for the deployment of numerous sensors throughout the factory, enabling continuous monitoring of different areas. This widespread sensor coverage facilitates a comprehensive view of the entire production environment.
- Cloud-Based Platforms: Data collected from IoT devices is often transmitted to cloud-based platforms for storage, analysis, and visualization. Cloud platforms provide centralized data storage and allow for real-time monitoring and reporting.
Data Visualization Tools
Data visualization tools are essential for effectively interpreting the large volume of data collected from IoT devices. These tools enable manufacturers to identify patterns, trends, and potential issues in their operations.
- Dashboards: Interactive dashboards provide a graphical representation of key performance indicators (KPIs) and real-time data, allowing for immediate visibility into the status of manufacturing processes. They enable a user-friendly overview of critical data.
- Charts and Graphs: Charts and graphs visually represent data trends and patterns, such as machine performance over time, allowing for analysis of historical data and prediction of future trends. These visual representations allow for effective interpretation and comparison of data.
- Heatmaps and Maps: These tools visualize data distribution across different areas of the factory, allowing for identification of hotspots or areas requiring attention. This visual representation helps in quickly identifying and addressing problem areas.
Comparison of Data Collection Methods
Method | Description | Pros | Cons |
---|---|---|---|
Industrial Ethernet | High-speed network for data transmission | Fast data transfer, real-time monitoring, high reliability | Requires significant infrastructure investment, potential for network failures |
Wireless Sensor Networks (WSNs) | Deployment of numerous sensors for comprehensive coverage | Flexible deployment, continuous monitoring of multiple locations | Potential for signal interference, limited data transmission rate in some cases |
Cloud-Based Platforms | Centralized data storage and analysis | Scalability, data security, access from anywhere | Potential for latency, dependence on internet connectivity |
Predictive Maintenance and Optimization
Leveraging IoT data in manufacturing allows for proactive maintenance strategies, shifting from reactive repairs to preventative actions. This approach minimizes downtime, reduces maintenance costs, and improves equipment lifespan. By anticipating potential equipment failures, manufacturers can schedule maintenance effectively, ensuring consistent production and maximizing output.
Predictive maintenance utilizes sensor data from connected equipment to identify patterns and anomalies that signal impending failures. Sophisticated algorithms analyze this data to forecast potential issues and trigger timely maintenance interventions. This proactive approach significantly reduces unplanned downtime and enhances overall operational efficiency.
IoT in manufacturing is rapidly changing production lines, but the same principles can be applied elsewhere. For instance, the digital transformation in education, like Digitizing education , can borrow from the efficiency gains seen in automated manufacturing processes. Ultimately, these digital advancements, whether in the classroom or on the factory floor, promise to boost productivity and innovation across the board.
Methods for Analyzing Sensor Data
Analyzing sensor data involves identifying trends, anomalies, and patterns that indicate potential equipment failures. Machine learning algorithms are frequently employed to process vast amounts of data, recognizing subtle changes that might otherwise be missed. This includes techniques like statistical process control (SPC), which monitors deviations from established norms, and pattern recognition, which identifies unusual data sequences. Time series analysis, which studies data over time, is crucial in anticipating equipment failures based on historical trends.
Examples of Successful Predictive Maintenance Implementations
Numerous manufacturing companies have successfully implemented predictive maintenance strategies. For example, a turbine manufacturer used IoT sensors to monitor vibration levels, temperature, and pressure within their turbines. By analyzing this data with machine learning algorithms, they were able to predict potential bearing failures well in advance. This allowed for scheduled maintenance, avoiding costly unplanned shutdowns. Similarly, a packaging company utilized IoT sensors on their conveyor belts to track strain and stress levels.
Early detection of anomalies allowed for preventative maintenance, ensuring smooth operation and high output.
Predictive Maintenance Algorithms
Algorithm | Description | Advantages | Disadvantages |
---|---|---|---|
Statistical Process Control (SPC) | Monitors deviations from established norms to identify trends indicative of potential failure. | Simple to implement, widely understood, and often inexpensive. | May not capture complex relationships, requires careful parameter tuning, and might not detect subtle anomalies. |
Machine Learning (ML) -Regression | Uses historical data to model relationships between sensor data and equipment health. | Can capture complex relationships, adaptable to new data, and can predict future failures with higher accuracy. | Requires large amounts of training data, prone to overfitting if not carefully managed, and can be computationally intensive. |
Machine Learning (ML) -Anomaly Detection | Identifies data points that deviate significantly from the expected behavior. | Effective in detecting unusual events, can alert to unforeseen issues, and requires less training data compared to regression models. | Can be less accurate in predicting failures, often requires significant data preprocessing, and may generate false positives. |
Time Series Analysis | Studies data over time to identify patterns and predict future behavior. | Excellent for detecting gradual degradation, useful for long-term prediction, and effective in capturing trends. | Complex models may be needed for non-linear or unpredictable patterns, might require significant computational resources, and can be difficult to interpret. |
Automation and Process Improvement
IoT integration significantly enhances automation in manufacturing processes, leading to improved efficiency and productivity. By connecting machines, equipment, and systems, manufacturers gain real-time insights into operational parameters, enabling proactive adjustments and streamlined workflows. This interconnectedness fosters a more dynamic and responsive manufacturing environment, capable of adapting to changing demands and optimizing resource allocation.
IoT-driven automation goes beyond simple tasks, facilitating intricate process improvements that were previously difficult or impossible to achieve manually. This automation empowers manufacturers to focus on higher-level strategic initiatives, further boosting profitability and competitiveness.
Automated Tasks Enabled by IoT
Real-time data from sensors embedded in machinery allows for automated adjustments to production parameters. This capability translates into optimized performance and reduced waste. Automated quality control processes, triggered by sensor data, ensure consistent product quality and reduce defects, minimizing rework and costs. Predictive maintenance, facilitated by IoT, anticipates equipment failures, enabling proactive maintenance schedules, preventing costly downtime.
Enhanced Supply Chain Visibility and Control
IoT facilitates greater transparency and control throughout the supply chain. Real-time tracking of materials, inventory, and shipments allows for improved visibility and proactive management of potential bottlenecks. This visibility helps manufacturers to optimize inventory levels, reducing storage costs and minimizing material shortages. By monitoring the entire journey of goods, manufacturers can better anticipate demand fluctuations and adjust production schedules accordingly, minimizing delays and improving overall supply chain responsiveness.
This comprehensive oversight significantly strengthens the supply chain’s resilience to disruptions. For example, real-time tracking of raw materials from origin to manufacturing facilities enables manufacturers to identify and mitigate risks related to quality, delays, or logistical issues early in the process, avoiding costly problems later.
Impact on Efficiency and Productivity
Automation, enabled by IoT, directly translates into increased efficiency and productivity. Automated processes reduce human error, minimizing the risk of defects and rework. Optimized resource allocation, enabled by real-time data, reduces waste and increases output. For instance, automated adjustments to machine parameters in response to changing conditions maximize production throughput and minimize downtime. Predictive maintenance further enhances efficiency by preventing unplanned equipment failures, reducing the time lost due to unexpected breakdowns.
Security and Privacy Considerations
Implementing IoT in manufacturing brings significant benefits, but also introduces new security vulnerabilities. Protecting sensitive data and ensuring the integrity of manufacturing processes is paramount. A robust security framework is crucial to mitigate risks and maintain operational efficiency.
Protecting sensitive data within manufacturing environments using IoT technologies requires a comprehensive approach. This includes understanding the potential threats, implementing robust security protocols, and establishing clear security policies.
Security Risks Associated with IoT Implementation
Manufacturing environments, now increasingly reliant on IoT devices, are exposed to various security risks. These include unauthorized access to control systems, data breaches, and potential disruptions to production processes. Compromised equipment can lead to operational downtime, financial losses, and even safety hazards. Malicious actors could potentially manipulate critical processes, leading to dangerous outcomes.
Security Protocols for IoT Data Protection
Several security protocols are essential for safeguarding data transmitted and stored by IoT devices. These protocols aim to ensure data confidentiality, integrity, and availability. Robust authentication mechanisms are vital for verifying the identity of devices and users. Data encryption protects sensitive information during transmission and storage. Secure communication channels are required for transmitting data between devices and control systems.
- Authentication: Implementing strong authentication protocols, such as multi-factor authentication (MFA), is crucial to verify the identity of users and devices. This prevents unauthorized access to sensitive data and manufacturing processes. Example: Requiring both a username/password and a one-time code from a mobile device to log into a manufacturing control system.
- Data Encryption: Encrypting data both in transit and at rest is essential. This protects sensitive information from unauthorized access, even if intercepted. Example: Using encryption protocols like TLS/SSL for secure communication between IoT devices and servers.
- Secure Communication Channels: Using secure communication channels, such as VPNs (Virtual Private Networks), is critical for transmitting data between devices and control systems. Example: Establishing a VPN connection between a factory’s IoT devices and its central data servers to ensure secure communication.
- Access Control: Implementing access control lists (ACLs) and role-based access control (RBAC) limits access to specific data and functionalities based on user roles. Example: Granting different levels of access to different employees, such as read-only access for quality control personnel versus full access for engineers.
Framework for Implementing Robust Security Measures
A robust security framework for IoT-enabled manufacturing systems requires a multi-layered approach. This includes the development of a comprehensive security policy, regular security audits, and employee training. The framework should also incorporate incident response procedures and ongoing monitoring.
- Security Policy Development: A clearly defined security policy Artikels the rules and procedures for handling security threats. This policy should address data handling, access controls, and incident response.
- Regular Security Audits: Regular security audits are essential to identify and address potential vulnerabilities. These audits should assess the effectiveness of security controls and ensure compliance with industry standards.
- Employee Training: Training employees on security best practices is critical to fostering a security-conscious culture. This training should cover the risks of cyber threats and how to identify and report suspicious activities.
- Incident Response Procedures: Establish clear procedures for handling security incidents. This includes steps to contain the damage, investigate the cause, and recover from the incident.
- Continuous Monitoring: Implement ongoing monitoring of the system to detect and respond to security threats in real-time. This includes continuous monitoring of logs, security alerts, and system performance.
Creating a Comprehensive Security Policy
A comprehensive security policy for an IoT-enabled manufacturing environment should cover various aspects, including access control, data encryption, and incident response. This policy should be reviewed and updated regularly to reflect evolving threats and best practices.
A comprehensive security policy is a living document that needs to be adapted and improved over time.
Integration with Existing Systems
Integrating IoT systems seamlessly into existing manufacturing infrastructures is crucial for realizing the full potential of Industry 4.0. This integration often presents challenges, but careful planning and strategic implementation can mitigate these issues and unlock significant operational improvements. Successful integration hinges on understanding the existing systems and tailoring the IoT solution to complement them rather than replace them.
Integrating IoT solutions requires a thorough understanding of the existing manufacturing processes and data flows. This involves identifying key data points, defining the required data formats, and establishing clear communication channels between the IoT devices and the existing infrastructure. Careful consideration of security protocols and data governance is paramount throughout this process.
Challenges in Integration
Existing manufacturing environments often comprise a complex network of legacy systems, disparate data formats, and potentially incompatible communication protocols. Addressing these differences requires a phased approach to integration, often involving custom interfaces and data transformation processes. Data silos can also hinder integration efforts, preventing a holistic view of the manufacturing process.
Strategies for Integration
A key strategy involves modular design for the IoT system. This approach allows for incremental integration, minimizing disruption to existing operations and facilitating a smooth transition. Implementing standardized communication protocols, such as MQTT or OPC UA, can simplify data exchange between IoT devices and legacy systems. Developing robust data mapping and transformation processes is essential to ensure compatibility between disparate data formats.
Integrating IoT Platforms with ERP Systems
Integrating IoT platforms with Enterprise Resource Planning (ERP) systems allows for real-time data synchronization and enhanced decision-making. This integration enables the ERP system to access data from IoT devices, providing a comprehensive view of the manufacturing process. The result is improved inventory management, production scheduling, and overall operational efficiency. For example, real-time tracking of inventory levels based on IoT sensors can lead to proactive adjustments in supply chain management within the ERP system.
Successful Integration Examples
Several successful integrations have been observed in diverse manufacturing settings. A semiconductor manufacturer, for example, integrated IoT sensors into their assembly line, allowing real-time monitoring of critical parameters. This data was fed into their ERP system, enabling predictive maintenance and optimized resource allocation. Another example comes from a logistics company that integrated IoT tracking devices into their fleet management system, enabling real-time monitoring of delivery routes and optimized delivery schedules.
Integrating IoT Devices with Legacy Control Systems
Seamless integration of IoT devices with legacy control systems requires careful consideration of the existing communication protocols and data formats. Often, custom interfaces or middleware solutions are necessary to bridge the gap between the IoT devices and legacy systems. This process can involve implementing gateways that translate data between different communication protocols. For example, a food processing plant integrated IoT sensors with their existing SCADA system to monitor environmental conditions and adjust production parameters in real-time.
This ensured consistent quality and safety standards.
Future Trends and Developments
The integration of IoT in manufacturing is rapidly evolving, driven by the continuous advancement of technologies like AI and machine learning. These advancements are enabling more sophisticated data analysis, predictive capabilities, and automated processes, transforming traditional manufacturing paradigms. This evolution promises significant improvements in efficiency, productivity, and overall operational performance.
IoT in manufacturing is rapidly evolving, impacting everything from production efficiency to supply chain management. This directly affects customer experience technology, as seamless operations translate into faster delivery times and higher quality products. Ultimately, robust IoT systems in manufacturing are key to delivering a positive customer experience, which in turn fuels future growth in the sector. Customer experience technology is crucial for understanding and meeting consumer needs.
The future of IoT in manufacturing is marked by a convergence of technologies, leading to more interconnected and intelligent factories. This interconnectedness allows for real-time data sharing, improved decision-making, and enhanced collaboration among various departments and systems. Manufacturers are actively exploring new avenues for optimizing their operations and gaining a competitive edge in the market.
Emerging Technologies Impacting IoT in Manufacturing
The landscape of manufacturing is undergoing a significant transformation, driven by the integration of cutting-edge technologies. These technologies are reshaping the way factories operate, leading to increased efficiency, improved quality, and reduced costs.
- Artificial Intelligence (AI) and Machine Learning (ML): AI and ML are increasingly playing a critical role in analyzing vast amounts of data generated by IoT devices. This analysis enables the identification of patterns, trends, and anomalies that can be used to optimize processes, predict equipment failures, and improve overall production efficiency. For example, AI-powered systems can analyze sensor data from various machines to identify potential maintenance issues before they cause costly downtime.
- Edge Computing: Edge computing brings processing power closer to the source of data, enabling real-time analysis and decision-making. This reduces latency, improves responsiveness, and enhances the efficiency of IoT systems in manufacturing environments. It also allows for faster responses to critical events.
- 5G and other High-Speed Networks: The adoption of high-speed, low-latency networks like 5G is crucial for supporting the increasing data volume generated by IoT devices in manufacturing. These advanced networks ensure seamless communication and real-time data transmission between devices and systems, allowing for more agile and responsive operations.
- Blockchain Technology: Blockchain can enhance the security and transparency of IoT systems in manufacturing by providing a secure and immutable record of transactions and data. This is particularly valuable for tracking products, managing supply chains, and ensuring product authenticity.
Potential Future Applications of IoT in Manufacturing
The potential applications of IoT in manufacturing are diverse and far-reaching. These applications are driving increased productivity, efficiency, and profitability for manufacturers.
- Enhanced Predictive Maintenance: IoT-enabled systems can monitor equipment health in real-time, enabling predictive maintenance strategies. This proactive approach minimizes downtime, reduces maintenance costs, and extends the lifespan of equipment.
- Smart Supply Chain Management: Real-time tracking of goods and materials throughout the supply chain, enabled by IoT, can optimize logistics, reduce delays, and improve inventory management. This real-time visibility allows for proactive adjustments in response to changes.
- Automated Quality Control: IoT sensors and devices can monitor product quality parameters in real-time, ensuring that products meet stringent quality standards. This proactive approach prevents defects from reaching the end customer, enhancing product quality.
Advanced IoT Technologies in Manufacturing
Numerous advanced IoT technologies are currently being implemented in manufacturing settings. These technologies are revolutionizing manufacturing processes, leading to significant improvements in efficiency and productivity.
- Industrial Robotics: IoT-connected robots can be programmed and controlled remotely, enhancing flexibility and productivity in manufacturing lines. These robots can adapt to changing production needs and perform tasks with greater precision.
- Smart Factories: The concept of a smart factory involves the integration of IoT devices, systems, and processes to create a highly interconnected and intelligent manufacturing environment. This approach allows for real-time monitoring and control of production, enabling optimized resource allocation.
- 3D Printing Integration: IoT devices can monitor the 3D printing process, optimizing parameters and ensuring consistent product quality. This allows for better control over the manufacturing process and improved production outcomes.
Evolving Role of AI and Machine Learning in IoT-Driven Manufacturing
AI and machine learning are becoming integral components of IoT-driven manufacturing, enabling more sophisticated data analysis and automation. These technologies are driving a new era of intelligent manufacturing.
- Improved Decision-Making: AI and ML algorithms can analyze vast amounts of data generated by IoT devices to identify patterns, predict outcomes, and make data-driven decisions for optimizing manufacturing processes.
- Enhanced Automation: AI-powered systems can automate complex tasks, reduce human error, and improve the efficiency of manufacturing operations. This results in higher output and better control over production.
Case Studies of Successful IoT Implementations
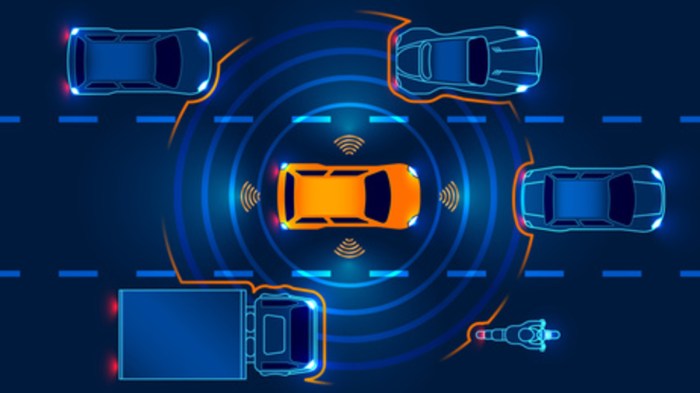
Industrial manufacturing has witnessed a surge in the adoption of Internet of Things (IoT) solutions. These implementations are transforming operations, leading to significant improvements in efficiency, productivity, and profitability. Analyzing successful deployments provides valuable insights for other companies considering similar initiatives.
Illustrative Examples of Successful IoT Implementations
Numerous companies have successfully integrated IoT technologies into their manufacturing processes. These deployments often involve collecting real-time data from various sources, enabling enhanced monitoring, predictive maintenance, and process optimization.
Case Study 1: Predictive Maintenance in a Turbine Manufacturing Company
A turbine manufacturer, using sensors embedded in their production machinery, collected data on vibration, temperature, and pressure. This data was analyzed using sophisticated algorithms to predict potential equipment failures. By proactively addressing potential issues, the company minimized downtime and avoided costly repairs. This led to a 15% reduction in maintenance costs and a 10% increase in production output.
Case Study 2: Real-Time Inventory Management in a Logistics Company
A logistics company used IoT sensors to track the location and condition of inventory in real-time. This allowed for improved supply chain management, reduced inventory carrying costs, and enabled proactive responses to potential disruptions. The system enabled the company to optimize its warehousing space and improve delivery schedules, increasing customer satisfaction.
Case Study 3: Smart Manufacturing in an Automotive Component Supplier
An automotive component supplier implemented IoT solutions across its entire manufacturing facility. This included integrating sensors into assembly lines, robots, and quality control equipment. By collecting and analyzing data from these sources, the company was able to identify bottlenecks in the production process, optimize resource allocation, and improve overall production quality. This resulted in a significant decrease in production errors, leading to higher product quality and reduced rework costs.
Key Takeaways from Case Studies
Company | Industry | Solution | Results |
---|---|---|---|
Turbine Manufacturer | Energy | Predictive maintenance using sensor data | 15% reduction in maintenance costs, 10% increase in production output |
Logistics Company | Logistics | Real-time inventory tracking using sensors | Improved supply chain management, reduced inventory carrying costs, optimized warehousing space, improved delivery schedules |
Automotive Component Supplier | Automotive | Comprehensive IoT implementation across the facility | Significant decrease in production errors, higher product quality, reduced rework costs |
Global Market Overview
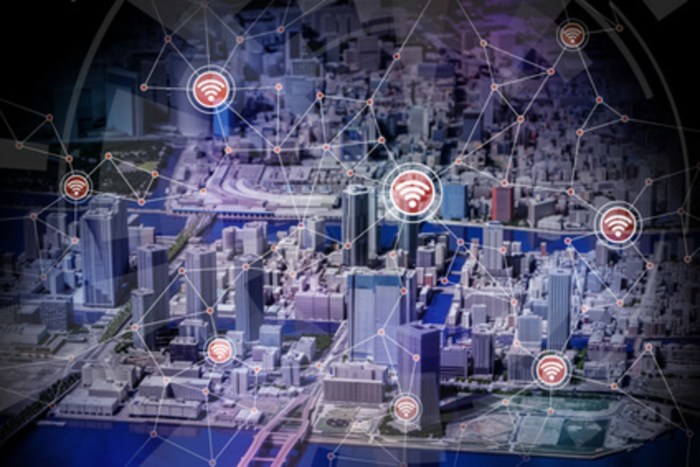
The global market for IoT solutions in manufacturing is experiencing substantial growth, driven by the increasing need for efficiency, productivity, and predictive capabilities in industrial processes. This expansion is fuelled by advancements in sensor technology, cloud computing, and data analytics, all converging to create a powerful ecosystem for optimizing manufacturing operations.
The widespread adoption of IoT in manufacturing is transforming traditional production models, allowing manufacturers to gather real-time data, analyze trends, and proactively address potential issues. This leads to significant cost savings and enhanced competitiveness in the global marketplace.
Market Size and Projections
The global IoT manufacturing market is a significant segment of the broader industrial IoT market. While precise figures vary depending on the specific reporting agency, estimates place the current market size in the tens of billions of dollars, with projected growth in the double-digit percentage range over the next several years. This substantial growth is anticipated to continue as more manufacturers recognize the value proposition of IoT in optimizing their operations.
Major Players and Trends
A multitude of companies are contributing to the growth of the IoT manufacturing sector. These include established industrial automation players, specialized IoT solution providers, and cloud-based data analytics companies. Key trends include the increasing adoption of edge computing for real-time data processing, the rise of Industry 4.0 principles, and the integration of AI-driven predictive maintenance solutions.
Growth Potential and Challenges
The growth potential of IoT in manufacturing is substantial, with numerous avenues for optimizing production processes and improving profitability. The potential for significant cost reductions, increased output, and enhanced quality control is substantial. However, challenges remain, including the high initial investment required for implementation, the complexity of integrating diverse systems, and the need for robust cybersecurity measures to protect sensitive data.
For example, successful implementations often require specialized expertise in industrial networks and data management.
Key Regions
The adoption of IoT solutions in manufacturing varies across different geographical regions. North America and Western Europe currently lead in adoption, driven by established manufacturing infrastructure and a readily available skilled workforce. However, Asia-Pacific, particularly China, is rapidly catching up, showing strong growth potential due to its large manufacturing base and burgeoning digital economy. Other regions are also experiencing increasing adoption rates, albeit at different paces, influenced by factors such as economic development, regulatory environments, and technological infrastructure.
Epilogue
In conclusion, IoT in manufacturing represents a paradigm shift in how businesses operate. By integrating smart technologies and data-driven insights, manufacturers can gain a competitive edge and achieve significant returns on investment. The future of manufacturing is undoubtedly intertwined with IoT, promising a more efficient, sustainable, and productive industry. Challenges remain, but the potential benefits of this technology are substantial.
FAQ Insights: IoT In Manufacturing
What are some common security risks associated with IoT in manufacturing?
Security breaches are a significant concern with IoT systems. Compromised devices can disrupt operations, lead to data loss, and potentially expose sensitive information. Unauthorized access, malware infections, and denial-of-service attacks are all potential threats. Strong security protocols and robust security measures are crucial to mitigate these risks.
How can manufacturers effectively integrate IoT platforms with existing ERP systems?
Successful integration often requires careful planning and a phased approach. Identifying the key data points and establishing clear communication protocols between the IoT platform and ERP system are crucial steps. Choosing the right integration tools and utilizing expert consultants can ensure a smooth transition and avoid compatibility issues.
What are the key factors to consider when calculating the ROI of an IoT implementation?
ROI calculations for IoT implementations should consider both tangible and intangible benefits. Quantify cost savings from reduced downtime, improved efficiency, and enhanced quality. Evaluate the potential for increased revenue and market share. Consider the long-term value of data-driven insights and the potential for innovation.
What emerging technologies will impact the future of IoT in manufacturing?
The future of IoT in manufacturing will be significantly influenced by advancements in AI, machine learning, and 5G connectivity. These technologies will enable more sophisticated data analysis, predictive capabilities, and real-time decision-making. The ability to handle massive amounts of data and rapidly respond to changing conditions will become increasingly important.