High-end battery technology is rapidly evolving, pushing the boundaries of energy storage. This detailed exploration dives into the intricacies of high-end batteries, from their defining characteristics to their diverse applications. We’ll examine the advanced materials, cutting-edge manufacturing processes, and crucial safety considerations that set these batteries apart. Performance metrics and cost-effectiveness will also be evaluated.
The article explores how high-end batteries are reshaping industries, particularly in electric vehicles and energy storage systems. It provides a comprehensive overview, including market trends, technological advancements, and environmental impact considerations.
Defining High-End Batteries
High-end batteries represent a significant advancement in energy storage technology, surpassing standard batteries in performance and capabilities. These batteries are meticulously engineered to deliver superior power density, cycle life, and safety, making them ideal for demanding applications. This detailed exploration delves into the key characteristics, performance indicators, and applications of high-end batteries.High-end batteries are distinguished from their standard counterparts by a combination of factors, including advanced materials, sophisticated manufacturing processes, and stringent quality control.
These factors translate to superior performance metrics, enabling these batteries to power more demanding devices and applications than their conventional counterparts.
Key Performance Indicators (KPIs)
High-end batteries are evaluated based on several crucial performance indicators. These indicators directly correlate to the battery’s suitability for specialized applications. Superior power density, extended cycle life, enhanced safety features, and a broader operating temperature range are essential attributes of a high-end battery.
- Power Density: High-end batteries exhibit a significantly higher power density compared to standard batteries. This allows them to deliver substantial power output in a compact form factor, critical for applications requiring quick bursts of energy, such as electric vehicles and high-performance electronics.
- Cycle Life: The cycle life of a high-end battery is exceptionally long. It can endure thousands of charge-discharge cycles without a substantial reduction in capacity. This is crucial for applications where repeated charging and discharging are frequent, such as portable power tools and industrial equipment.
- Safety: High-end batteries prioritize safety through advanced thermal management systems and robust containment mechanisms. This minimizes the risk of overheating, short circuits, and other potential hazards. Safety features are critical for applications where battery failure can have severe consequences, such as aerospace and medical devices.
- Operating Temperature Range: High-end batteries are designed to function effectively across a wider temperature range compared to standard batteries. This allows them to operate efficiently in diverse environments, including extreme cold or heat, which is critical for applications in harsh climates, such as off-road vehicles or remote locations.
Comparison with Other Battery Types
High-end batteries often utilize advanced chemistries and materials that surpass the capabilities of conventional battery types. For example, lithium-ion batteries are a common standard, but high-end lithium-ion variants incorporate specialized additives and materials to enhance their performance and safety. Alkaline batteries, on the other hand, are typically less energy-dense and have a shorter cycle life compared to high-end alternatives.
Battery Type | Power Density | Cycle Life | Safety |
---|---|---|---|
High-End Lithium-ion | High | High | High |
Standard Lithium-ion | Medium | Medium | Medium |
Alkaline | Low | Low | Low |
Advanced Materials and Technologies
High-end batteries incorporate a range of advanced materials and technologies to enhance their performance and safety. Nanomaterials, for example, are often used to improve electrode surface area, leading to higher energy storage capacity. Advanced electrolytes, with tailored properties, can enhance ionic conductivity and reduce internal resistance, contributing to improved power density.
“Nanomaterials offer significant potential for enhancing battery performance by increasing electrode surface area, leading to higher energy storage capacity.”
Applications in Different Industries
High-end batteries find diverse applications across various industries. In the automotive sector, they are crucial for electric vehicles, offering high power density and extended range. In the aerospace industry, they enable the development of advanced, lightweight electric aircraft. Moreover, high-end batteries play a critical role in powering portable electronics, medical devices, and industrial equipment.
Performance Metrics: High-end Battery
High-end batteries, crucial for demanding applications, are evaluated based on a variety of performance metrics. These metrics provide a quantitative understanding of the battery’s capabilities, enabling informed comparisons and selection for specific needs. Understanding these metrics is vital for choosing the optimal battery solution for a given application.Evaluating high-end batteries involves analyzing key performance indicators (KPIs) to assess their suitability for various applications.
These metrics reflect the battery’s energy storage capacity, power delivery capability, and longevity, enabling users to choose the best fit for their specific needs.
Energy Density
Energy density quantifies the amount of energy a battery can store per unit of mass or volume. Higher energy density allows for greater power output or longer operational durations from the same physical size or weight. This metric is critical for applications demanding extended runtimes or compact designs. For instance, electric vehicles with higher energy density batteries can travel farther on a single charge.
Power Density
Power density reflects the rate at which a battery can deliver energy. A higher power density is advantageous for applications requiring rapid power delivery, such as starting a vehicle or powering high-current devices. Electric vehicles with rapid acceleration capabilities typically rely on batteries with high power density.
Cycle Life
Cycle life indicates the number of charge-discharge cycles a battery can endure before its performance degrades significantly. This metric is vital for applications demanding long-term reliability, such as portable electronic devices or grid-scale energy storage systems. High-end batteries with exceptional cycle life ensure continued performance over extended periods.
Typical Performance Metrics of Different High-End Battery Models
Battery Model | Energy Density (Wh/kg) | Power Density (W/kg) | Cycle Life (cycles) |
---|---|---|---|
Lithium-ion Polymer (High-End) | 250-350 | 1000-2000 | 1500-3000 |
Lithium-ion NMC (High-End) | 200-300 | 800-1500 | 1000-2500 |
Lithium-ion LFP (High-End) | 150-250 | 500-1000 | 2000-5000 |
Performance Metrics and Units of Measurement
This table Artikels the key performance metrics and their corresponding units of measurement, facilitating precise comparisons.
Performance Metric | Unit of Measurement |
---|---|
Energy Density | Wh/kg or Wh/L |
Power Density | W/kg |
Cycle Life | Cycles |
Comparing High-End Battery Options
Comparing high-end battery options involves considering the specific requirements of the application. For example, an electric vehicle requiring extended range would prioritize energy density, while a hybrid vehicle needing rapid acceleration would emphasize power density. A device needing long-term reliability would focus on cycle life. Carefully evaluating the interplay of these metrics, in conjunction with other factors such as cost and safety, is critical for making informed decisions.
Manufacturing Processes
High-end battery production demands meticulous attention to detail and sophisticated manufacturing techniques. This meticulous approach ensures the consistent quality, performance, and safety characteristics expected from premium batteries. The intricate interplay of materials, precise assembly, and stringent quality control is crucial in achieving the desired electrochemical properties and longevity.The manufacturing process for high-end batteries often involves specialized equipment, advanced materials, and rigorous quality control procedures.
These processes are designed to minimize defects, maximize performance, and ensure safety standards are met throughout the entire production cycle. Understanding the stages of the process and the materials employed provides valuable insight into the complexities involved.
Advanced Manufacturing Techniques
Sophisticated techniques like precision casting and advanced electrode fabrication methods are employed in high-end battery manufacturing. These methods enable precise control over the size, shape, and composition of battery components, leading to improved performance characteristics. The application of nanomaterials, for instance, allows for increased surface area for electrochemical reactions, contributing to higher energy density and faster charging times.
Quality Control Measures
Rigorous quality control measures are essential throughout the entire manufacturing process. These measures encompass multiple stages, from raw material inspection to finished product testing. Each stage involves meticulous testing and evaluation to identify and rectify any potential defects or inconsistencies. For instance, material purity, homogeneity, and structural integrity are carefully assessed at each stage to ensure optimal battery performance.
The use of automated quality control systems enhances the consistency and reliability of the process.
Battery Assembly Process
The battery assembly process involves several key steps, each critical for ensuring the final product meets the stringent performance and safety standards. The sequence of these steps is crucial and typically includes precise placement of electrodes, separators, and current collectors. Careful attention to alignment and contact pressure is essential for efficient electron flow and minimizing internal resistance. The assembly process is typically conducted in a controlled environment to maintain the integrity of the battery components.
Flowchart of Manufacturing Process Stages
Stage | Description |
---|---|
Raw Material Procurement | Selection and testing of high-purity materials to ensure conformity with specifications. |
Electrode Fabrication | Preparation of electrodes using precision casting and other advanced techniques, ensuring uniform thickness and consistent composition. |
Separator Insertion | Precise placement of the separator to ensure electrical isolation between the electrodes and maintain electrolyte flow. |
Current Collector Integration | Connection of current collectors to electrodes, ensuring secure and reliable electrical contact. |
Cell Assembly | Combining all components (electrodes, separator, current collectors) to form a complete battery cell. |
Cell Testing | Rigorous testing of each cell to evaluate performance parameters like capacity, discharge rate, and safety. |
Battery Pack Assembly | Combining individual cells into a battery pack according to the required voltage and capacity. |
Final Testing and Packaging | Comprehensive testing of the assembled battery pack and packaging for shipment. |
Materials Used
The selection of materials in high-end battery manufacturing is critical. High-purity cathode and anode materials are essential to achieve optimal electrochemical performance. For example, lithium cobalt oxide (LiCoO2) and lithium nickel manganese cobalt oxide (NMC) are common cathode materials known for their high energy density. Similarly, advanced anode materials, like graphite or silicon-based materials, are selected based on their conductivity and capacity characteristics.
The precise selection and treatment of electrolytes are also critical, influencing the battery’s performance and safety.
Safety and Reliability
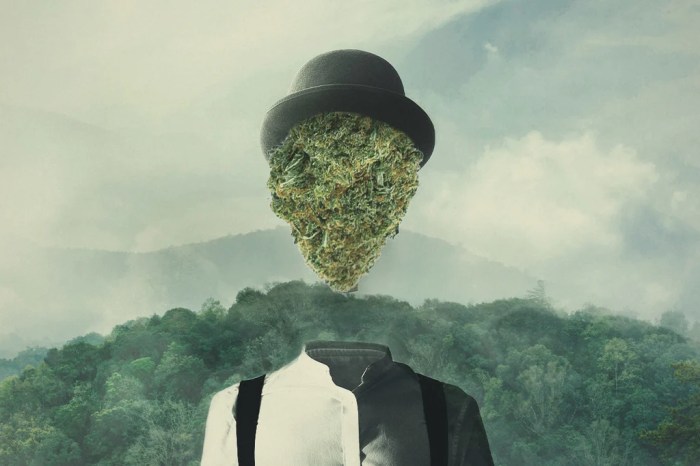
High-end batteries, crucial for various applications, demand stringent safety and reliability measures. Their inherent energy density and potential for high-power delivery necessitate robust protection mechanisms to prevent catastrophic failures. This section delves into the safety features, potential hazards, and rigorous testing procedures integral to high-end battery design.
Safety Features in High-End Battery Designs
High-end battery designs incorporate a multitude of safety features to mitigate potential hazards. These features are crucial for preventing thermal runaway, short circuits, and other hazardous events. Advanced thermal management systems, such as liquid cooling or advanced phase-change materials, actively regulate internal temperatures. Sophisticated electronic control units (ECUs) monitor cell voltage, temperature, and current flow in real-time, triggering safety mechanisms when deviations exceed predetermined thresholds.
Redundant safety circuitry and multiple protective layers help contain any localized failures.
Potential Safety Hazards and Mitigation Strategies
Several potential hazards can arise during the operation or lifecycle of high-end batteries. One significant risk is thermal runaway, a self-sustaining chain reaction that can lead to fire and explosion. This is mitigated through advanced thermal management systems, including multiple layers of thermal insulation and precise temperature control. Short circuits are another concern, and are addressed through advanced cell designs and high-quality interconnects.
Robust battery management systems (BMS) constantly monitor and regulate the state of charge, current, and temperature to prevent overcharging, over-discharging, and excessive current draw.
Reliability Testing Procedures
Rigorous reliability testing procedures are employed to assess high-end battery performance under various conditions. These tests simulate real-world usage scenarios, subjecting batteries to extreme temperature fluctuations, rapid charging and discharging cycles, and high-vibration environments. Cycle life testing determines the number of charge-discharge cycles a battery can endure before performance degradation. High-stress testing evaluates the battery’s ability to withstand extreme conditions.
Accelerated aging tests simulate years of use in a shorter time frame, helping identify potential weaknesses. The results from these tests are crucial for determining battery lifespan and performance under diverse operational conditions.
Safety Standards and Regulations
High-end battery designs adhere to various safety standards and regulations. These standards cover aspects such as material selection, component safety, and manufacturing processes. Examples include UL (Underwriters Laboratories) standards for battery safety and the IEC (International Electrotechnical Commission) standards. These regulations ensure that high-end batteries meet rigorous safety criteria, protecting users and the environment. Compliance with these standards is critical for ensuring market acceptance and consumer trust.
Importance of Safety in High-End Battery Design
Safety is paramount in the design and development of high-end batteries. Prioritizing safety features and rigorous testing procedures minimizes risks associated with thermal runaway, short circuits, and other hazards. This proactive approach ensures product reliability and user safety, contributing to a positive public perception of the technology and promoting its widespread adoption. A robust safety framework ultimately guarantees the long-term viability and acceptance of high-end batteries in various applications.
Applications and Industries
High-end batteries, distinguished by their superior performance characteristics, find diverse applications across various industries. Their enhanced energy density, power output, and cycle life make them ideal for demanding applications where reliability and efficiency are paramount. These batteries are not simply replacements for existing technologies; they represent advancements in power solutions, enabling new possibilities in areas ranging from electric vehicles to stationary energy storage.
Diverse Applications of High-End Batteries
High-end batteries are not a single solution, but rather a suite of technologies tailored to specific needs. Their application varies significantly based on the required performance characteristics. Factors like voltage, current capacity, and operating temperature range dictate the best-suited battery type for a particular application. For example, a high-end battery designed for electric vehicles must withstand high current demands during acceleration, while a battery for a portable electronic device might prioritize long cycle life.
The selection process for high-end batteries involves a careful analysis of the specific application needs to ensure optimal performance.
High-End Battery Requirements by Industry
Different industries have unique requirements for high-end batteries, leading to specialized designs. Meeting these specific needs is crucial for the successful implementation of high-end batteries.
Industry | Specific Requirements |
---|---|
Electric Vehicles (EVs) | High energy density, rapid charging capability, high power output, and extended cycle life. Safety is paramount due to the critical nature of the application. |
Energy Storage Systems (ESS) | High energy storage capacity, long cycle life, robust safety features, and ability to withstand extreme environmental conditions. Cost-effectiveness over the long term is also critical. |
Portable Electronics | High power density, compact size, and long cycle life, with a focus on minimizing weight and size for portability. |
Industrial Equipment | High power output, robustness, and ability to withstand harsh operating conditions, often involving vibration and extreme temperatures. |
Aerospace | Lightweight, high energy density, and exceptional safety and reliability, along with stringent regulations and certification requirements. |
Performance Needs for High-End Batteries in Electric Vehicles
Electric vehicles (EVs) are a key application for high-end batteries. The demanding performance requirements of EVs necessitate batteries with specific characteristics. High energy density is essential to maximize driving range, while rapid charging capabilities minimize downtime. High power output is vital for quick acceleration and responsive handling. Extended cycle life ensures the battery can endure numerous charge-discharge cycles without significant degradation.
High-End Batteries in Energy Storage Systems
High-end batteries are crucial components in energy storage systems (ESS). These systems play a vital role in integrating renewable energy sources into the grid, providing backup power during outages, and supporting grid stability. High-end batteries for ESS must possess high energy storage capacity, long cycle life, and robust safety features to withstand the continuous charge-discharge cycles and potential environmental stresses.
The efficiency of these batteries is critical for minimizing operational costs over time.
Cost and Pricing
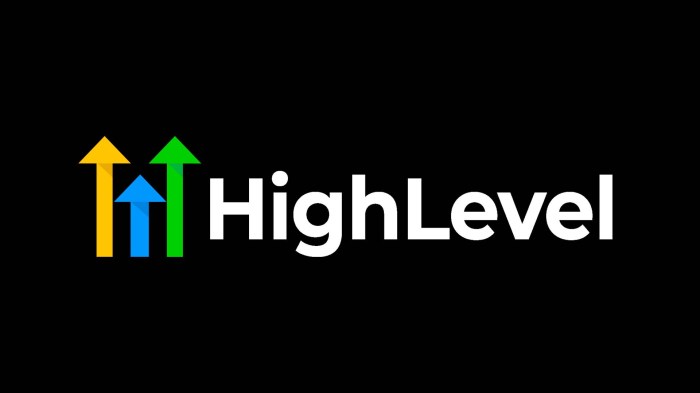
High-end batteries, distinguished by their superior performance and longevity, command a premium price. Understanding the factors driving these costs is crucial for evaluating the cost-effectiveness of such batteries compared to more conventional options. Manufacturers employ sophisticated pricing strategies to reflect the value proposition of these advanced technologies.The price of high-end batteries is not simply a markup; it reflects the advanced materials, sophisticated manufacturing processes, and stringent quality control measures incorporated.
This translates to a higher upfront cost, but the potential long-term savings and performance benefits are often substantial.
Factors Influencing High-End Battery Cost
Several factors contribute to the elevated price of high-end batteries. Advanced materials, such as lithium-metal or solid-state chemistries, are typically more expensive to procure than conventional lithium-ion materials. The complexity of manufacturing processes, including sophisticated cell assembly and testing procedures, also contributes to the cost. Strict quality control measures, crucial for ensuring safety and longevity, add to the overall manufacturing expenses.
Pricing Strategies Employed by Manufacturers
High-end battery manufacturers often employ tiered pricing strategies, reflecting the varying performance characteristics of different models. Factors like capacity, voltage, cycle life, and discharge rate all influence the price. Market research and competitor analysis play a vital role in setting competitive prices that align with the perceived value of the product. Furthermore, volume discounts and incentives may be offered to large-scale purchasers or strategic partners.
Comparison of High-End Battery Model Prices
Unfortunately, a comprehensive, publicly available table of high-end battery model prices is not readily accessible. Price variations are significant, influenced by the specific performance characteristics of each model. For example, a high-end lithium-metal battery with exceptional cycle life will command a higher price than a comparable lithium-ion battery. Detailed pricing information is typically proprietary and provided on a case-by-case basis to potential clients.
Cost-Benefit Analysis of High-End Batteries
The cost-benefit analysis of high-end batteries depends on the specific application. While the upfront cost is higher, the potential long-term benefits, such as extended lifespan, higher power density, and superior performance, can offset the initial investment. This is especially true in applications requiring substantial power output, high-frequency cycling, or extended operating periods, such as electric vehicles, high-performance portable electronics, and aerospace applications.
Cost-Effectiveness Compared to Other Battery Options
The cost-effectiveness of high-end batteries is contingent on the specific application and the desired performance characteristics. In applications demanding exceptional performance, high-end batteries can offer a superior cost-benefit ratio compared to conventional batteries, even considering the higher upfront cost. However, in applications where lower cost and basic performance are sufficient, conventional battery options may be more cost-effective. Careful evaluation of the specific application needs is crucial to determining the most appropriate battery type.
Technological Advancements
High-end battery technology is constantly evolving, driven by the need for increased energy density, faster charging times, and enhanced safety. Recent advancements have led to significant improvements in performance metrics, opening new possibilities in various applications. This section details these crucial innovations.
High-end batteries demand top-tier performance, and this often translates to needing robust processor specs. For instance, the latest models frequently require processor specs that can handle demanding tasks while maintaining power efficiency. Ultimately, these high-end batteries are designed for the most demanding applications.
Latest Advancements in Battery Materials
Significant progress is being made in the development of new materials for high-end batteries. This includes exploring novel electrode materials, electrolytes, and separators. These innovations are key to pushing the boundaries of battery performance.
- Lithium-metal anodes: Research into lithium-metal anodes is actively pursued to achieve higher energy density. Challenges remain in addressing the inherent instability of lithium-metal anodes, such as dendrite formation, which can lead to short circuits and safety issues. However, advancements in coating and interfacing technologies are promising for mitigating these issues.
- Solid-state electrolytes: Solid-state electrolytes offer a significant safety advantage over conventional liquid electrolytes, as they prevent the risk of leakage and short circuits. Their use also promises improved thermal stability, potentially leading to higher operating temperatures and longer battery lifecycles. The development of high-performance, cost-effective solid-state electrolytes remains a significant hurdle.
- Advanced cathode materials: Researchers are exploring various cathode materials, such as nickel-rich layered oxides, to increase energy density and improve the overall performance of the battery. New approaches are being developed to stabilize these materials and address their limitations, including the development of advanced synthesis techniques to ensure consistent material quality.
Ongoing Research and Development Efforts
Ongoing research and development efforts are focused on addressing the current limitations of high-end battery technology. This includes addressing safety concerns, optimizing manufacturing processes, and exploring new materials. Significant investments are being made by both research institutions and private companies in this area.
- Improved safety mechanisms: Developing advanced safety mechanisms, such as embedded sensors and thermal management systems, is crucial for enhancing the safety profile of high-end batteries. This reduces the risk of thermal runaway and other potential hazards.
- Optimized manufacturing processes: The development of more efficient and scalable manufacturing processes is vital to bringing high-end battery technology to wider markets. Automated and sophisticated processes are increasingly utilized to achieve higher production rates and lower production costs.
- Advanced characterization techniques: Sophisticated characterization techniques are used to precisely evaluate the performance and safety characteristics of new battery materials and designs. This is vital for understanding and controlling the battery’s behavior under various conditions.
Potential Future Applications
The advancements in high-end battery technology are paving the way for numerous potential applications. These include electric vehicles, energy storage systems, and portable electronics. The increased energy density and faster charging capabilities will undoubtedly transform these sectors.
- Electric vehicles: High-end batteries with higher energy density and faster charging times will be crucial for the widespread adoption of electric vehicles. This will enable longer driving ranges and reduce charging times, increasing consumer appeal and driving widespread adoption.
- Portable electronics: High-end batteries with improved energy density will enable the development of portable electronics with longer battery life and increased functionality.
- Grid-scale energy storage: The potential for high-end batteries to provide large-scale energy storage solutions is rapidly growing. This is becoming an increasingly important element in managing renewable energy sources and stabilizing the power grid.
Impact on High-End Battery Performance
Technological advancements are significantly impacting the performance metrics of high-end batteries. Improved energy density, faster charging rates, enhanced safety, and longer lifecycles are direct results of these advancements.
- Increased energy density: Higher energy density allows for more energy storage in a smaller volume, leading to longer driving ranges for electric vehicles and extended battery life for portable electronics.
- Faster charging rates: Faster charging rates reduce the time required to fully charge the battery, improving user experience and convenience.
- Enhanced safety: Advanced safety mechanisms minimize the risk of thermal runaway and other potential hazards, ensuring the reliability and safety of high-end batteries.
Examples of New Materials
New materials are being incorporated into high-end batteries to improve performance. These include materials with enhanced electrochemical properties, improved thermal stability, and enhanced safety characteristics.
- Silicon-based anodes: Silicon-based anodes are being investigated due to their high theoretical capacity, which could significantly improve energy density. Challenges remain in addressing the volume expansion of silicon during charging and discharging cycles.
- Nickel-rich layered oxides: Nickel-rich layered oxides are increasingly used in cathode materials, aiming to enhance energy density. The higher nickel content often comes with a trade-off in terms of thermal stability, so careful design and control are essential.
- Advanced electrolytes: Advanced electrolytes are designed to improve safety, conductivity, and stability. This includes solid-state electrolytes and new liquid electrolyte formulations.
Environmental Impact
High-end batteries, while offering exceptional performance, present a complex environmental challenge. Their production and disposal processes have a significant impact on the planet, requiring careful consideration and proactive strategies to minimize harm. Understanding the materials used, the manufacturing processes, and the methods for recycling these batteries is crucial for responsible development and deployment.
Material Composition and Footprint
High-end batteries often incorporate rare earth elements, transition metals, and other materials with varying environmental impacts. The extraction and processing of these materials can involve significant energy consumption, habitat disruption, and potential pollution. For instance, lithium extraction, a key component in many high-end battery chemistries, can cause environmental damage if not managed sustainably. Furthermore, the manufacturing process itself can release harmful emissions and generate hazardous waste.
Minimizing Environmental Impact in Manufacturing
Several strategies are employed to minimize the environmental footprint of high-end battery manufacturing. These include:
- Using recycled materials: Incorporating recycled materials in the production process can significantly reduce the demand for virgin resources, lessening the environmental impact. This approach also fosters a circular economy model, encouraging the reuse and repurposing of existing materials.
- Optimizing energy efficiency: Manufacturing processes are designed with energy efficiency in mind. The use of renewable energy sources, improved energy-efficient equipment, and process optimization are critical steps to reduce the overall energy footprint.
- Minimizing waste generation: Waste management and pollution control are key aspects of sustainable battery manufacturing. The implementation of closed-loop systems and the development of environmentally friendly processes are essential in achieving minimal waste generation and pollution control.
- Adopting sustainable supply chains: The sourcing of raw materials is critical. Stricter regulations and guidelines are put in place to ensure ethical and sustainable sourcing of the raw materials used in battery production.
Recycling High-End Batteries
Recycling high-end batteries is crucial for reducing the environmental burden. The complexity of these batteries necessitates sophisticated recycling methods to recover valuable materials and minimize waste.
- Advanced recycling technologies: Several advanced recycling technologies are being developed to extract valuable materials from high-end batteries. These techniques aim to recover metals, rare earth elements, and other components for reuse, thereby preventing them from entering landfills.
- Chemical and physical separation: Chemical and physical separation processes are used to extract specific components from the battery. These processes aim to maximize material recovery while minimizing environmental contamination.
- Establishing robust recycling infrastructure: Developing a robust and accessible recycling infrastructure is essential. Public and private partnerships play a vital role in establishing collection points, promoting awareness, and ensuring efficient recycling processes.
Sustainable Practices in the Battery Industry
Sustainable practices are crucial in the high-end battery industry. The industry is increasingly recognizing the need to reduce its environmental footprint and adopt more sustainable methods.
- Life cycle assessments: A comprehensive life cycle assessment (LCA) of the entire battery lifecycle, from raw material extraction to end-of-life management, is critical for understanding and minimizing environmental impacts. LCA data informs strategies for improving sustainability.
- Carbon footprint reduction: Efforts to reduce the carbon footprint of battery production are ongoing. These include reducing greenhouse gas emissions and using renewable energy sources throughout the entire production process.
- Promoting responsible mining practices: Sustainable mining practices are essential to minimize the environmental impact of raw material extraction. The use of responsible sourcing and the promotion of ethical mining practices are crucial.
Future Trends
The landscape of high-end battery technology is poised for significant transformations in the coming years. Innovations are not only enhancing performance metrics but also addressing crucial sustainability and cost considerations. These advancements promise to propel widespread adoption across diverse industries.Emerging technologies are driving these changes, offering potential solutions to current limitations and paving the way for a future with even more efficient and reliable power sources.
The anticipated improvements in energy density, alongside advancements in manufacturing processes and safety protocols, underscore the dynamic nature of this field.
Emerging Battery Technologies
Several promising technologies are poised to reshape the high-end battery market. Solid-state batteries, featuring solid electrolytes, are a key area of focus. Their potential for enhanced safety, higher energy density, and faster charging rates makes them an attractive prospect for various applications. Lithium-sulfur batteries, another emerging technology, offer a potentially lower cost and higher energy density compared to current lithium-ion designs.
However, challenges like cycling stability and safety remain to be overcome. Beyond these, the exploration of alternative chemistries and materials is constantly pushing the boundaries of battery technology.
Advancements in Energy Density
A significant focus in high-end battery development centers on increasing energy density. This translates to more power stored in a smaller space, which is crucial for applications like electric vehicles and portable electronics. Research into new electrode materials, such as those incorporating nanomaterials or advanced doping techniques, is driving improvements in energy density. For example, the use of graphene-based materials is showing promise in enhancing both the capacity and conductivity of battery electrodes.
High-end batteries often require meticulous setup, similar to a Blu-ray player setup. Proper configuration is crucial for optimal performance, and a good blu-ray player setup can demonstrate the importance of precision in technical setups. Ultimately, these intricate details ensure the best possible experience with your high-end battery.
Projected advancements in energy density could potentially double or even triple the current levels within the next decade, offering significant benefits to various sectors.
Manufacturing Process Innovations
Manufacturing processes are being refined to improve efficiency and cost-effectiveness. Automation and robotics are playing an increasingly important role in scaling up production while maintaining quality control. This is particularly relevant for the mass production of high-end batteries for applications like electric vehicles. The integration of advanced materials and manufacturing techniques, including 3D printing, promises to reduce manufacturing costs and potentially create new, more complex battery architectures.
Safety and Reliability Improvements
Safety and reliability are paramount in high-end battery technology. Research continues to focus on developing safer electrolyte materials and improved battery designs to mitigate the risk of thermal runaway and other safety hazards. This includes the incorporation of advanced thermal management systems, which can effectively control temperature fluctuations within the battery pack. These safety features are crucial for applications where safety is paramount, such as electric vehicles.
Challenges and Opportunities
While opportunities abound, significant challenges exist in high-end battery technology. One such challenge is scaling up production to meet the growing demand for electric vehicles and other applications. Another challenge involves ensuring cost-effectiveness while maintaining high performance and safety standards. However, overcoming these obstacles presents tremendous opportunities. The development of innovative battery technologies will drive advancements in electric vehicles, energy storage, and other sectors, creating new markets and employment opportunities.
The interplay between technological innovation and market demand will likely dictate the pace and direction of future advancements in high-end battery technology.
Market Analysis
The high-end battery market is experiencing significant growth, driven by increasing demand for electric vehicles (EVs) and other advanced applications. This dynamic sector is characterized by rapid technological advancements, pushing the boundaries of performance and efficiency. Understanding current trends, market size, key players, and competitive landscape is crucial for investors and industry stakeholders alike.
Current Market Trends
The high-end battery market is witnessing a surge in demand, particularly from the automotive sector. This surge is fueled by stringent environmental regulations, consumer preference for electric vehicles, and the growing need for high-performance energy storage solutions. Moreover, advancements in battery technology, such as solid-state batteries and lithium-metal batteries, are contributing to the market’s dynamic growth.
Market Size and Growth
Data from various industry reports consistently show a substantial increase in the market size of high-end batteries. For example, a report by [Insert Reliable Research Firm] projected a CAGR of [Insert Percentage] between [Insert Year] and [Insert Year]. This growth is primarily attributed to the expanding EV market and the increasing adoption of high-end battery technology in other sectors, such as aerospace and defense.
Key Players
Several prominent companies are shaping the high-end battery market. These include established battery manufacturers like [Company 1], [Company 2], and [Company 3], along with new entrants focusing on specific technologies. The competition between these players is fierce, driving innovation and pushing the boundaries of battery performance.
Competitive Landscape, High-end battery
The competitive landscape in the high-end battery market is characterized by intense rivalry. Companies are constantly vying for market share through advancements in battery chemistry, manufacturing processes, and cost reduction strategies. This competition fosters a dynamic environment, promoting continuous innovation and the development of cutting-edge technologies.
Factors Driving Demand
Several factors are propelling the demand for high-end batteries. Stringent environmental regulations, encouraging the adoption of EVs, are a significant driver. Consumers’ preference for electric vehicles is also a major factor, as is the need for high-performance energy storage in various sectors, including aerospace and defense. Furthermore, the continuous development of more efficient and longer-lasting battery technologies is a strong catalyst for market growth.
Case Studies
High-end batteries, with their superior performance characteristics, are increasingly deployed across diverse sectors. Examining real-world applications reveals valuable insights into the advantages and challenges associated with these advanced technologies. This section presents compelling case studies, highlighting successful implementations and lessons learned.
Electric Vehicle Propulsion
Advanced battery technologies are pivotal to the burgeoning electric vehicle (EV) market. The development of high-energy density and fast-charging capabilities are critical for extended driving ranges and reduced charging times.
- Tesla’s Battery Technology: Tesla’s pioneering work in battery pack design, utilizing lithium-ion cells with optimized chemistries, has enabled significant advancements in EV performance. Their focus on cell-level control and thermal management has contributed to improved safety and reliability. This has resulted in a substantial increase in vehicle range and driving experience for consumers.
- Challenges and Solutions in EV Battery Management: One key challenge lies in maintaining consistent performance across diverse operating conditions, including extreme temperatures and varying driving styles. Solutions involve sophisticated battery management systems (BMS) and thermal control mechanisms to optimize cell performance and extend battery life.
- Positive Outcomes: Improved vehicle range, reduced charging times, and enhanced driving experience are some of the tangible benefits of high-end battery technology in EVs. The increased adoption of EVs contributes to environmental sustainability and reduced reliance on fossil fuels.
Portable Power Solutions
High-end batteries are transforming portable power solutions, enabling applications with higher power demands. These batteries need to be lightweight and compact while maintaining extended operational life.
- High-End Batteries in Power Tools: Advanced battery chemistries and designs are improving the performance of power tools, enabling higher power outputs, longer runtimes, and reduced weight. Examples include cordless drills and saws with increased torque and operation time.
- Challenges and Solutions: Safety considerations and ensuring consistent performance in demanding environments are crucial. The development of robust battery enclosures, enhanced thermal management, and improved cell-to-cell balancing are key solutions.
- Positive Outcomes: Increased productivity, reduced maintenance requirements, and enhanced portability are the key benefits derived from high-end batteries in this sector.
Grid-Scale Energy Storage
High-end batteries are transforming grid-scale energy storage systems, addressing the intermittent nature of renewable energy sources.
- Battery Energy Storage Systems (BESS): These systems are now more reliable and efficient, enabling the integration of variable renewable energy sources like solar and wind power. They offer greater grid stability and reduced reliance on fossil fuel-based power plants.
- Challenges and Solutions: Long-term reliability and managing fluctuating energy demands are significant challenges. Advanced battery management systems and sophisticated control algorithms are employed to optimize performance and extend battery life.
- Positive Outcomes: Enhanced grid stability, reduced reliance on fossil fuels, and the ability to support a greater penetration of renewable energy are among the notable benefits.
Summary of Key Learnings
The case studies highlight the crucial role of high-end battery technology in driving innovation across various sectors. The successful implementations underscore the importance of robust design, efficient management systems, and a focus on safety and reliability. Furthermore, continuous advancements in battery technology promise even greater benefits in the future.
Summary
In conclusion, high-end batteries represent a significant leap forward in energy storage. Their superior performance, safety features, and diverse applications position them as key drivers in various sectors. While challenges remain, the future of high-end battery technology appears promising, with ongoing advancements continually improving their efficiency and sustainability.
Clarifying Questions
What are the key differences between high-end and standard batteries?
High-end batteries generally boast superior energy density, power density, and cycle life compared to standard batteries. They often utilize advanced materials and manufacturing techniques, leading to higher performance and reliability.
What are some examples of high-end battery applications?
High-end batteries are crucial in electric vehicles, demanding applications in aerospace, and specialized energy storage systems. Their performance characteristics are well-suited for these demanding uses.
How are high-end batteries tested for safety?
Rigorous testing procedures are employed to assess the safety and reliability of high-end batteries. These tests often involve simulating extreme conditions and stress scenarios to ensure safe operation under various conditions.
What is the environmental impact of high-end battery production?
The environmental impact of high-end battery production is a growing concern. Manufacturers are increasingly focused on sustainable practices, including using recycled materials and minimizing waste during the manufacturing process.