Sensor technology underpins countless modern innovations, from sophisticated medical equipment to cutting-edge automotive systems. This guide dives deep into the world of sensors, exploring their diverse types, applications, and underlying technologies. We’ll examine the crucial steps in sensor design, calibration, and integration, providing a comprehensive understanding of this essential technology.
Understanding the intricacies of sensor technology is paramount for anyone seeking to develop, implement, or utilize these critical components. From basic principles to advanced applications, this guide will serve as a valuable resource for both students and professionals alike.
Sensor Types and Applications
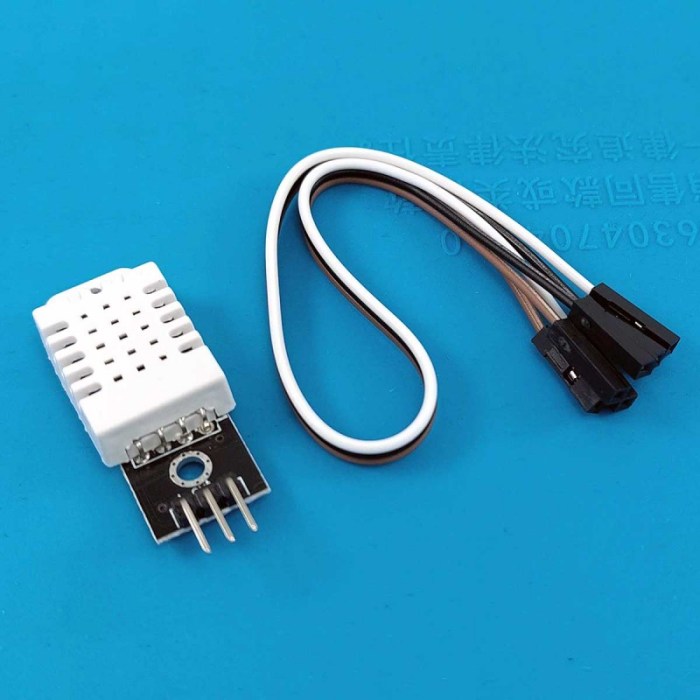
Sensors are crucial components in a vast array of applications, transforming physical phenomena into electrical signals that can be processed and interpreted by systems. They form the bridge between the physical world and the digital realm, enabling automation, control, and monitoring across diverse industries. This section delves into the classification of sensors, highlighting their applications and the physical phenomena they measure.
Furthermore, it offers a comparative analysis of temperature sensors, showcasing their strengths and weaknesses.
Sensor Classification
Understanding sensor types is fundamental to selecting the appropriate device for a specific application. Sensors can be categorized based on the physical phenomenon they measure, the technology they employ, or their application. The diverse range of sensor types allows for accurate and reliable measurement in various conditions and environments.
- Mechanical Sensors: These sensors measure mechanical quantities like displacement, force, pressure, and vibration. Examples include strain gauges, load cells, and accelerometers. Strain gauges, for instance, measure changes in length or deformation, finding applications in structural health monitoring and robotics. Load cells are used in weighing scales and industrial automation systems to monitor force or weight.
- Thermal Sensors: These sensors measure temperature, heat flow, or related thermal quantities. Examples include thermocouples, resistance temperature detectors (RTDs), and infrared (IR) thermometers. Thermocouples are widely used in industrial processes for continuous temperature monitoring, while RTDs offer high accuracy and stability in demanding environments.
- Optical Sensors: These sensors measure light, ranging from intensity to color. Examples include photodiodes, photoresistors, and CCD sensors. Photodiodes are essential in solar cells and optical communication systems, converting light energy into electrical current. CCD sensors are used in digital cameras and scientific imaging instruments to capture and process light.
- Chemical Sensors: These sensors measure the concentration of specific chemical substances in a medium. Examples include gas sensors, pH sensors, and conductivity sensors. Gas sensors are used in environmental monitoring, industrial safety, and medical diagnostics to detect various gases like carbon monoxide or ammonia. Conductivity sensors are used to measure the concentration of ions in water or other solutions.
Applications of Different Sensor Types
Sensors are indispensable tools across a multitude of industries. Their specific functionalities are tailored to the requirements of each application, ensuring accurate data collection and reliable control systems.
- Automotive Industry: Sensors are vital for various functions, including engine control, safety features (like airbags and anti-lock brakes), and driver assistance systems. Accelerometers and gyroscopes are used for vehicle stability control. Optical sensors are employed for proximity detection and parking assistance.
- Industrial Automation: Sensors enable precise control of machinery, monitoring process parameters, and ensuring product quality. Temperature sensors are crucial in maintaining optimal conditions for manufacturing processes. Pressure sensors are employed to monitor fluid levels and pressure within machinery.
- Environmental Monitoring: Sensors play a critical role in tracking environmental conditions, such as air quality, water quality, and weather patterns. Gas sensors are used to detect pollutants in the air, while water quality sensors monitor the presence of contaminants in water bodies.
Sensors by Measured Physical Phenomenon
Categorizing sensors by the physical phenomenon they measure provides a systematic overview of sensor capabilities.
- Temperature: Temperature sensors are used in a broad range of applications, from industrial processes to medical devices. Accurate temperature measurement is critical for ensuring optimal performance and safety.
- Pressure: Pressure sensors are essential for monitoring and controlling pressure in various systems, including hydraulic and pneumatic systems, and for measuring atmospheric pressure.
- Light: Light sensors are employed in applications such as photometry, astronomy, and robotics. They measure the intensity, wavelength, or other properties of light.
Comparison of Temperature Sensors
A comparison of temperature sensors reveals their respective strengths and weaknesses in different contexts.
Sensor Type | Strengths | Weaknesses |
---|---|---|
Thermocouple | Cost-effective, relatively simple | Limited accuracy, susceptible to thermal EMF |
RTD (Resistance Temperature Detector) | High accuracy, good stability, wide temperature range | More complex to implement, higher cost |
Thermistor | Fast response time, low cost | Lower accuracy compared to RTDs, limited temperature range |
Infrared Thermometer | Non-contact measurement, fast response time | Limited accuracy at low temperatures, susceptible to ambient radiation |
Sensor Technologies and Mechanisms
Different sensor types employ various technologies and mechanisms to detect and measure physical quantities. Understanding these underlying principles is crucial for selecting the appropriate sensor for a specific application. This section delves into the workings of different sensor types, offering explanations and analogies to aid comprehension.Different sensor technologies translate physical phenomena into electrical signals that can be processed and interpreted by a system.
This conversion process is the core function of any sensor, and the specific method employed varies depending on the physical quantity being measured. This allows us to design and implement sophisticated measurement systems across diverse fields.
Pressure Sensor Mechanisms
Pressure sensors measure the force exerted per unit area. Their design varies, but they all share the common goal of converting pressure changes into measurable electrical signals. A common type is the diaphragm pressure sensor, which utilizes a flexible diaphragm that deforms in response to pressure changes. This deformation is then translated into a change in electrical resistance or capacitance.
- The diaphragm, a thin, flexible membrane, is a crucial component in the pressure sensor. When pressure changes, the diaphragm deforms, either bulging or flattening.
- This deformation is detected by a measuring element, such as a strain gauge or a capacitive element. The strain gauge measures the change in length of the diaphragm. The capacitive element measures the change in the distance between the diaphragm and a fixed plate.
- The output signal from the measuring element is an electrical signal proportional to the pressure change. This signal is then processed by a system to display or record the pressure.
Optical Sensor Operating Principles
Optical sensors utilize light to detect and measure various physical quantities. Different types of optical sensors have unique operating principles, but they all rely on the interaction of light with the measured medium.
- Photoresistors, also known as light-dependent resistors (LDRs), are simple optical sensors that change their electrical resistance in response to changes in light intensity. An increase in light intensity decreases the resistance, and vice versa.
- Photodiodes convert light energy directly into an electrical current. The current produced is proportional to the intensity of the light striking the photodiode. This is commonly used in light meters and automatic cameras.
- Phototransistors amplify the current generated by photodiodes, making them more sensitive to light variations than photodiodes alone. They are used in more sophisticated optical sensing applications where higher sensitivity is required.
Comparison of Optical Sensor Types
Sensor Type | Operating Principle | Advantages | Disadvantages |
---|---|---|---|
Photoresistors | Resistance changes with light intensity. | Simple design, low cost. | Lower sensitivity compared to photodiodes or phototransistors. |
Photodiodes | Direct conversion of light into current. | Higher sensitivity than photoresistors. | Lower output current than phototransistors. |
Phototransistors | Amplified current from photodiodes. | High sensitivity and gain. | More complex circuitry required. |
Sensor Design and Development
Sensor design and development is a multifaceted process that involves meticulous planning, careful selection of materials, and rigorous testing. Successful sensor design hinges on a deep understanding of the target application, the desired performance characteristics, and the constraints imposed by the environment. This process requires a blend of scientific principles, engineering expertise, and iterative refinement.
Crucial Steps in Sensor Design
The design of a new sensor typically follows a structured approach. Initiation involves defining the sensor’s purpose and expected performance metrics, such as sensitivity, accuracy, and response time. This initial stage also identifies the key physical phenomena the sensor will utilize. Material selection is a critical step, carefully considering the material’s properties in relation to the sensing mechanism.
Furthermore, the design needs to be optimized for the specific operating environment, including temperature, pressure, and humidity ranges. Prototyping and testing are crucial to identify and refine potential design flaws, ultimately leading to a robust and reliable sensor.
Considerations for Environmental Conditions
Various environmental factors influence sensor performance. Temperature fluctuations, humidity levels, and pressure variations can significantly affect a sensor’s accuracy and stability. For example, a pressure sensor designed for high-altitude applications will require different materials and construction techniques compared to a sensor intended for use in a humid environment. Careful consideration of these conditions during the design phase is crucial to ensure the sensor’s long-term reliability.
Protecting the sensor from external influences is an important element in achieving its intended performance.
Sensor Development Flowchart
The development process for a sensor can be visualized as a flowchart. The process begins with defining the problem and specifications. This is followed by material selection, and design refinement. Next, the sensor is fabricated and tested under controlled conditions. After testing, adjustments are made based on the results, leading to an improved design.
This iterative process continues until the sensor meets the desired performance characteristics. The entire process can be visualized as a cyclical loop, allowing for continuous improvement and refinement.
+-----------------+ | Define Problem | +-----------------+ | | | v | v +-----------------+ +-----------------+ | Material Selection |----->| Design Refinement | +-----------------+ +-----------------+ | | | v | v +-----------------+ +-----------------+ | Fabrication |----->| Testing | +-----------------+ +-----------------+ | | | v | v +-----------------+ +-----------------+ | Evaluation |----->| Adjustments | +-----------------+ +-----------------+ | | | v | v +-----------------+ | Iteration | +-----------------+
Key Components of a Typical Sensor
A sensor typically comprises several key components, each contributing to its overall function.
Component | Function |
---|---|
Sensing Element | Detects the target physical quantity (e.g., temperature, pressure). |
Transducer | Converts the physical quantity into a measurable signal (e.g., electrical signal). |
Signal Conditioning Circuit | Amplifies, filters, and processes the transducer’s output signal to improve accuracy and reliability. |
Output Device | Displays or transmits the processed signal (e.g., digital display, data logger). |
Enclosure/Housing | Protects the internal components from the environment and provides mechanical support. |
Sensor Calibration and Validation
Sensor calibration and validation are crucial steps in ensuring the reliability and accuracy of sensor data. Proper calibration establishes a known relationship between the sensor’s output and the physical quantity being measured. Validation confirms that the sensor consistently produces accurate results within its specified operating range and under various conditions. These processes are essential for applications requiring precise measurements, where inaccurate data can lead to significant errors or even safety hazards.
Sensor Calibration Procedure
Calibration establishes a precise relationship between the sensor’s output and the corresponding physical quantity. A well-defined calibration procedure involves several steps. First, select a set of known input values (standards) covering the sensor’s expected operating range. These standards should be traceable to recognized national or international standards. Next, measure the sensor’s output for each input value.
Record the input and corresponding output values in a tabular format. This data is used to develop a calibration curve or equation that describes the relationship between input and output. A linear equation, a polynomial equation, or a more complex function may be appropriate depending on the sensor type and characteristics. Finally, validate the calibration curve by applying it to a set of independent input values.
The resulting outputs should closely match the expected outputs from the standards. Accurate calibration data is crucial for achieving precise measurements.
Methods for Validating Sensor Accuracy
Several methods can validate sensor accuracy. One method involves comparing the sensor’s output to a known reference standard. Another method is to utilize multiple sensors to measure the same quantity. If the outputs are similar, it suggests the sensor is performing correctly. Statistical analysis techniques like calculating the mean, standard deviation, and confidence intervals of the sensor’s measurements over time can identify any systematic errors or variations.
Using different sensors from the same manufacturer can also offer insight into the sensor’s consistency. Regular calibration and validation procedures can ensure that the sensor is operating within its specifications.
Potential Sources of Error in Sensor Measurements
Sensor measurements can be affected by several factors. Environmental conditions, such as temperature, humidity, and pressure, can influence the sensor’s output. Sensor aging and degradation can lead to inaccurate measurements over time. Improper installation or handling can also contribute to errors. Interferences from other physical fields, such as electromagnetic fields, can affect some sensors.
Finally, the sensor’s inherent limitations, like its resolution and range, can introduce uncertainties in the measurements. Understanding and minimizing these errors is vital for obtaining reliable data.
Ensuring Reliable Sensor Data
To ensure reliable sensor data, implement rigorous calibration and validation procedures. Use appropriate sensor types for specific applications, and ensure that sensors are properly maintained and stored. Employing shielding to minimize interference from external factors can significantly enhance accuracy. Regularly checking for signs of sensor degradation is essential for timely maintenance or replacement. Thorough documentation of calibration and validation results is crucial for traceability and future analysis.
Reliable sensor data is essential for accurate analysis and informed decision-making.
Sensor Data Acquisition and Processing
Acquiring and processing sensor data is a critical step in extracting meaningful information from the physical world. This involves meticulously capturing raw sensor readings and transforming them into usable data for analysis and interpretation. Effective data acquisition and processing are essential for accurate measurements, reliable decision-making, and efficient system operation.
Methods for Acquiring Sensor Data
The methods for acquiring sensor data are diverse, varying significantly based on the specific sensor type and the application environment. Crucially, the choice of acquisition method must align with the sensor’s capabilities and the desired data resolution.
- Analog-to-Digital Conversion (ADC): This method is fundamental to converting analog sensor signals into digital data suitable for computer processing. The ADC samples the analog signal at regular intervals, quantizing the amplitude to discrete digital levels. The accuracy and speed of the ADC are key factors in determining the quality of the acquired data.
- Sampling Techniques: Different sampling strategies, like uniform sampling and non-uniform sampling, significantly impact the accuracy and efficiency of data acquisition. Choosing the right sampling frequency is crucial to avoid aliasing, which can introduce errors and distort the acquired signal.
- Data Logging: This method involves storing sensor data over time. Real-time logging is essential for monitoring continuous processes, while periodic logging is useful for capturing data at specific intervals. The storage capacity and data transfer rate of the logging system are important considerations.
- Data Streaming: Real-time applications often use data streaming, where sensor data is transmitted directly to a processing system as it’s acquired. This is critical in applications demanding immediate response, such as industrial automation and environmental monitoring.
Techniques for Processing Sensor Data
Processing sensor data involves transforming raw measurements into meaningful information. This transformation often involves mathematical operations and algorithms to extract key parameters, identify trends, and filter out noise.
- Signal Filtering: Noise and unwanted fluctuations in sensor data can significantly affect the accuracy of analysis. Various filtering techniques, like moving average filters, low-pass filters, and high-pass filters, are used to reduce these disturbances. The choice of filter depends on the characteristics of the noise and the desired signal properties.
- Calibration and Correction: Sensor readings are often influenced by factors such as temperature and pressure. Calibration techniques are used to account for these influences, ensuring that the acquired data accurately reflects the actual physical parameter being measured. Mathematical models and look-up tables are often used in the calibration process.
- Data Transformation: Transforming data into different formats or representations can reveal underlying patterns or trends. Techniques like Fourier transforms and wavelet transforms can reveal frequency components or temporal details in the signal.
- Data Aggregation: Summarizing large datasets can be useful for analysis. Techniques like averaging, maximum/minimum calculation, and standard deviation computation condense information into key metrics.
Role of Signal Conditioning in Improving Sensor Data Quality
Signal conditioning circuits are crucial components in sensor systems. They prepare the sensor’s output signal for processing, enhancing its quality and reliability. This often involves amplifying weak signals, filtering out noise, and ensuring compatibility with the subsequent data acquisition system.
- Amplification: Weak sensor signals often require amplification to meet the input requirements of the data acquisition system. Appropriate gain settings are essential to avoid saturation or distortion.
- Filtering: Noise reduction is a crucial aspect of signal conditioning. Filters remove unwanted frequencies from the signal, improving the accuracy of the measurements.
- Isolation: Isolation circuits are used to protect the data acquisition system from electrical interference or ground loops, ensuring reliable measurements.
- Linearization: Sensors often exhibit non-linear responses. Linearization circuits are used to correct this non-linearity, providing a more accurate representation of the measured physical parameter.
Flowchart for Acquiring and Processing Data from a Temperature Sensor
- Sensor Measurement: The temperature sensor measures the ambient temperature.
- Signal Conditioning: The signal from the sensor is amplified and filtered to remove noise.
- Analog-to-Digital Conversion (ADC): The analog signal is converted to a digital signal.
- Data Logging: The digital data is logged to a data storage device.
- Data Processing: The logged data is analyzed for trends, anomalies, or other useful information.
- Data Visualization: The processed data is displayed graphically for easier interpretation.
Sensor Integration and Systems
Integrating sensors into larger systems is a crucial step in developing sophisticated and effective applications. This process often involves careful consideration of various factors, from the physical mounting of the sensor to the digital communication protocols used for data transfer. Successful integration depends on a thorough understanding of both the sensor’s capabilities and the demands of the overall system.
Methods for Sensor Integration
Various methods exist for integrating sensors into larger systems. These methods range from simple wiring connections to complex networked architectures. The best approach depends heavily on the specific sensor type, the desired data rate, the environmental conditions, and the overall system design. Common integration methods include direct wiring, using signal conditioning circuitry, implementing wireless communication protocols (like Wi-Fi or Bluetooth), and integrating sensors within embedded systems.
Challenges of Integrating Sensors from Different Manufacturers
Integrating sensors from different manufacturers presents significant challenges. Variations in output signals, communication protocols, and physical dimensions can complicate the integration process. For instance, one sensor might output data in a voltage format, while another uses a current loop. Ensuring compatibility and seamless data flow between disparate sensor technologies requires careful consideration and often necessitates specialized signal conditioning circuits.
Sensors are crucial for high-quality playback, especially in a top-tier Blu-ray player like this one. These intricate devices accurately capture the subtle details within the encoded data, ensuring a rich and immersive viewing experience. Advanced sensor technology is key to the overall performance of any top-notch Blu-ray player.
Furthermore, calibration procedures may differ, requiring adjustments to ensure data consistency across the integrated system.
Importance of Sensor Interoperability
Sensor interoperability is critical for building robust and reliable systems. Interoperable sensors share a common communication protocol and data format, enabling seamless data exchange and analysis. This eliminates the need for complex data translation and allows for easier integration with existing software platforms. For example, a system employing multiple sensor types for environmental monitoring (temperature, humidity, light) will benefit greatly from interoperability, allowing the different sensor readings to be easily combined into a unified picture of the environment.
Sensors are crucial in cameras, and a key aspect of modern low power DSLR cameras like the low power DSLR is optimizing power consumption. High-performance sensors are essential for image quality, and these advancements in low-power design allow for longer battery life while maintaining impressive image capture capabilities. Ultimately, sensor technology is the heart of any good camera.
Troubleshooting Integrated Sensors
Troubleshooting issues with integrated sensors can be complex. Troubleshooting involves systematically identifying the source of the problem. A systematic approach to troubleshooting includes:
- Checking the sensor’s power supply and connection. A faulty connection or insufficient power supply can lead to erratic readings or complete failure of the sensor.
- Verifying the sensor’s communication protocol. Mismatched protocols can prevent the system from receiving data. Ensure that the communication protocol is correctly configured on both the sensor and the system side.
- Assessing the environmental conditions. Environmental factors like temperature, humidity, or electromagnetic interference can affect sensor readings. Proper calibration and environmental considerations are key to accurate readings.
- Evaluating sensor data for anomalies. Unusual or inconsistent sensor readings can indicate a problem. This often requires examining the sensor’s output over time to identify patterns or deviations.
Sensor Reliability and Maintenance
Ensuring the consistent and accurate performance of sensors is crucial for many applications. Reliability is paramount in industrial processes, scientific research, and everyday devices. Maintaining sensor performance involves understanding the factors that can degrade their accuracy and lifespan, and implementing strategies to mitigate these effects.
A well-maintained sensor translates to reliable data, reducing errors and potential costly consequences. Regular maintenance and proactive strategies for extending sensor lifespan are key components of effective sensor management.
Factors Affecting Sensor Reliability
Several factors can negatively impact the reliability of a sensor. These factors often interact and amplify each other, creating complex challenges in maintaining performance. Understanding these factors is essential for proactive maintenance.
- Environmental Conditions: Temperature fluctuations, humidity, vibration, and exposure to corrosive substances can significantly degrade sensor performance and accuracy over time. Extreme temperatures, for instance, can lead to material degradation or changes in the sensor’s internal components, thus altering the readings.
- Manufacturing Defects: Imperfections in the sensor’s design or manufacturing process can lead to inherent inaccuracies or inconsistencies in the measurements. Poorly calibrated or misaligned components can also contribute to unreliable readings.
- Age and Wear: As a sensor ages, the materials and components within it can degrade, leading to drift in readings and a reduction in sensitivity. Mechanical wear, especially for sensors with moving parts, can lead to performance issues.
- Interference: External electromagnetic fields, noise, or other interfering signals can corrupt the sensor’s output, resulting in inaccurate measurements. The source of interference can range from nearby electrical equipment to environmental factors like lightning.
Maintenance Procedures for Different Sensor Types
Effective maintenance strategies vary depending on the specific sensor type. A structured approach tailored to each sensor’s unique characteristics and potential failure points is crucial.
- Temperature Sensors: Regular calibration checks are essential, especially for sensors operating in extreme temperature ranges. Physical inspection for any visible damage or signs of corrosion should be performed. Cleaning the sensor’s surface and ensuring proper mounting are also critical maintenance tasks.
- Pressure Sensors: Regular calibration and validation are necessary, as pressure readings can fluctuate due to environmental factors. Inspect the sensor’s connection points for leaks or damage. Lubrication and maintenance of any moving parts are also important.
- Flow Sensors: Cleaning the sensor’s flow path to prevent blockages and ensure accurate measurements is essential. Periodic calibration is necessary to account for potential changes in the flow characteristics. Regular checks for any signs of wear and tear in the sensor mechanism should be carried out.
Impact of Environmental Factors on Sensor Reliability
Environmental conditions play a crucial role in the long-term reliability of sensors. Changes in temperature, humidity, pressure, and other factors can significantly affect sensor performance.
- Temperature: Temperature fluctuations can cause the sensor’s material properties to change, leading to variations in output readings. High temperatures can accelerate material degradation, potentially shortening the sensor’s lifespan. Conversely, extremely low temperatures can impact the sensor’s functionality or increase its susceptibility to damage.
- Humidity: High humidity can lead to corrosion and other degradation processes in the sensor, affecting its accuracy and reliability. Moisture absorption can also lead to errors in readings.
- Vibration: Continuous vibration can cause mechanical stress on the sensor, potentially leading to damage and inaccurate readings. Vibration dampening techniques can improve the sensor’s reliability in such environments.
Extending Sensor Lifespan
Implementing preventive maintenance and operational best practices can significantly extend the lifespan of sensors. These methods contribute to higher reliability and reduce downtime.
- Regular Calibration: Regular calibration helps maintain accuracy and identify any drift in readings early on. Calibration schedules should be tailored to the specific sensor type and operating conditions.
- Proper Storage and Handling: Storing sensors in appropriate environments, protecting them from damage and contamination, and using proper handling procedures are crucial. Environmental factors, such as temperature and humidity, should be considered.
- Preventive Maintenance: Routine checks, cleaning, and lubrication can prevent premature failures and extend the operational life of the sensor. Preventive maintenance should be based on sensor specifications and operational conditions.
Sensor Applications in Specific Industries
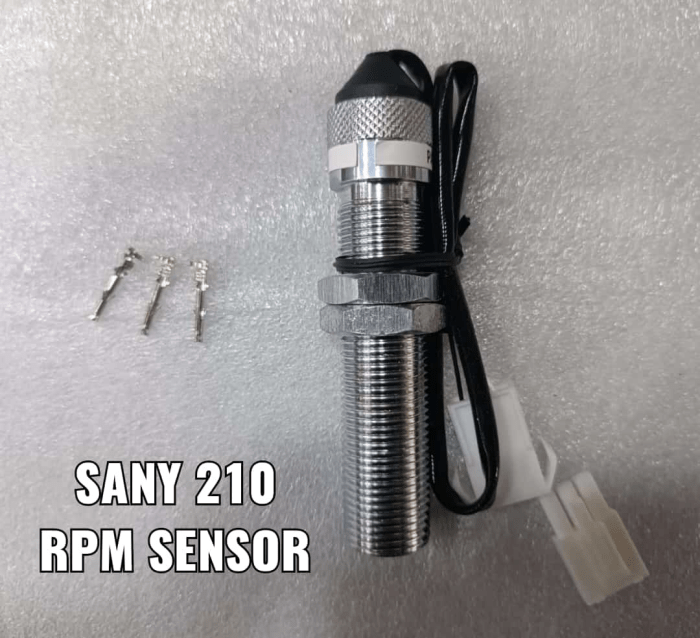
Sensors are indispensable tools across various industries, transforming how processes are managed and products are developed. Their ability to monitor, measure, and react to real-time data significantly improves efficiency, safety, and overall performance. From the intricate systems of automobiles to the delicate workings of medical equipment, sensors are fundamental to modern advancements.
Automotive Industry
Sensors play a crucial role in the modern automotive landscape, enhancing safety, performance, and fuel efficiency. They monitor a multitude of parameters, enabling advanced driver-assistance systems (ADAS) and critical vehicle functions.
- Engine Management: Sensors monitor parameters like engine temperature, air intake, and fuel pressure, allowing the engine control unit (ECU) to optimize performance and fuel consumption. This real-time feedback loop ensures smooth operation and minimizes emissions.
- Safety Systems: Crucial safety features like anti-lock braking systems (ABS), electronic stability control (ESC), and airbags rely heavily on sensor data. Sensors detect critical situations, such as sudden braking or loss of traction, and activate the appropriate safety mechanisms, potentially saving lives.
- Driver-Assistance Systems: Sensors like radar, ultrasonic, and cameras provide real-time information about the vehicle’s surroundings. This data is used to assist drivers with parking, lane departure warning, adaptive cruise control, and collision avoidance.
- Vehicle Diagnostics: Sensors continuously monitor various vehicle components and transmit data to the diagnostic system. This allows for proactive maintenance and early detection of potential issues, minimizing downtime and repair costs.
Medical Field
Sensors have revolutionized medical practices, enabling precise diagnosis, personalized treatment, and improved patient care. Their use spans from basic vital signs monitoring to complex surgical procedures.
- Vital Signs Monitoring: Sensors track heart rate, blood pressure, temperature, and oxygen saturation. This continuous monitoring is critical for patient care, especially in intensive care units (ICUs) or during surgeries. Real-time data enables immediate responses to changes in a patient’s condition.
- Surgical Robotics: Sensors in surgical robots provide precise positioning and movement, allowing surgeons to perform intricate procedures with enhanced accuracy and reduced invasiveness. This technology minimizes damage to surrounding tissues and promotes faster recovery times.
- Wearable Health Monitoring: Sensors embedded in wearable devices continuously track activity levels, sleep patterns, and other health metrics. This data can be used to monitor progress towards health goals and provide personalized feedback.
- Diagnostic Imaging: Sensors in medical imaging equipment, such as MRI and CT scanners, collect data that allows for detailed visualization of internal organs and structures. This data assists in diagnosing a wide range of conditions, enabling faster and more effective treatment plans.
Agriculture
Sensors are transforming agricultural practices, enabling data-driven decisions for optimal crop yields and resource management.
- Precision Agriculture: Sensors measure soil moisture, nutrient levels, and crop health. This data helps farmers tailor irrigation, fertilization, and pest control strategies to specific areas within a field, maximizing resource use and minimizing environmental impact.
- Livestock Monitoring: Sensors monitor animal health, such as heart rate, body temperature, and activity levels. This data enables proactive intervention, preventing disease outbreaks and optimizing livestock management practices.
- Weather Monitoring: Sensors provide real-time data on weather conditions, such as temperature, rainfall, and humidity. This data helps farmers anticipate potential weather-related risks and make informed decisions about crop management and livestock care.
Aerospace Industry
Sensors are essential for navigation, flight control, and safety in the aerospace industry. They provide critical data for various flight phases.
- Flight Control Systems: Sensors like accelerometers, gyroscopes, and altimeters provide crucial information for maintaining aircraft stability and control during flight. This real-time feedback allows pilots and flight control systems to react to changing conditions and maintain a safe trajectory.
- Navigation Systems: GPS receivers and inertial navigation systems rely on sensors to determine the aircraft’s position and velocity. This data enables accurate navigation and precise positioning for both commercial and military applications.
- Environmental Monitoring: Sensors monitor external factors like air pressure, temperature, and humidity. This data helps aircraft operate efficiently and safely in diverse environments. Understanding these factors improves the performance and lifespan of the aircraft.
- Safety Systems: Sensors are crucial for safety features such as collision avoidance systems. This data enables the system to detect potential hazards and take appropriate action to prevent accidents.
Future Trends and Innovations in Sensors
The field of sensor technology is experiencing rapid evolution, driven by advancements in materials science, microelectronics, and data processing. This dynamic environment promises increasingly sophisticated sensors with enhanced capabilities, paving the way for novel applications across diverse industries. The integration of these advancements with existing technologies will shape the future of various sectors, from healthcare to environmental monitoring.
Emerging Trends in Sensor Technology
Several key trends are shaping the future of sensor development. These include the miniaturization of sensors, leading to more compact and integrated systems; the emergence of wireless sensor networks, enabling the monitoring of remote and distributed environments; and the increasing use of advanced materials for improved sensitivity and performance. Furthermore, the integration of artificial intelligence (AI) and machine learning (ML) algorithms with sensor data is enabling more sophisticated analysis and interpretation.
Innovative Sensor Designs and Applications
Numerous innovative sensor designs are emerging, pushing the boundaries of what’s possible. One example is the development of flexible and wearable sensors, capable of monitoring physiological parameters continuously and non-intrusively. These sensors are revolutionizing healthcare by enabling personalized and proactive health management. Another exciting development is the creation of sensors for the detection of subtle changes in environmental parameters, enabling more precise and timely responses to environmental threats.
For instance, advanced acoustic sensors can detect early signs of earthquakes or structural damage in buildings.
Impact of New Materials and Technologies
The development of new materials plays a crucial role in driving sensor innovation. Materials with enhanced conductivity, piezoelectric properties, or optical characteristics are enabling the creation of sensors with improved sensitivity, accuracy, and robustness. For example, graphene-based sensors demonstrate exceptional sensitivity to various physical stimuli. Moreover, nanotechnology is also contributing significantly to the creation of highly sensitive sensors with miniature dimensions.
Nanomaterials, such as quantum dots, offer enhanced optical properties and enable the creation of highly sensitive optical sensors for various applications. The development of new materials like conductive polymers or composites is also contributing to the creation of flexible and wearable sensors with improved performance.
Predictions for the Future of Sensor Technology
The future of sensor technology is characterized by greater integration, miniaturization, and sophistication. Predictably, sensors will become increasingly pervasive in our daily lives, monitoring our health, our environment, and our infrastructure. For instance, the development of smart homes is heavily reliant on sensors for monitoring energy consumption and optimizing comfort levels. Moreover, the development of autonomous vehicles relies on sophisticated sensors for perception, navigation, and decision-making.
Furthermore, advancements in sensor technology are expected to play a crucial role in enabling the creation of more efficient and sustainable energy systems. The integration of sensors with artificial intelligence is expected to revolutionize various industries, leading to more autonomous and intelligent systems.
Sensor Safety and Regulatory Considerations
Safe sensor deployment is crucial, not only for the intended function but also for the protection of personnel and the environment. Understanding the specific safety measures associated with different sensor types and adhering to relevant regulations is paramount. This section details safety protocols, regulatory requirements, and legal considerations surrounding sensor systems.
Safety Measures for Specific Sensor Types
Different sensor types present unique safety hazards. For example, pressure sensors used in industrial settings require careful handling to avoid accidental injury from high-pressure releases. Similarly, chemical sensors used in environmental monitoring might expose personnel to hazardous substances if proper safety precautions are not followed. The risk assessment for each sensor type should encompass potential physical harm, chemical exposure, and electrical shock.
Regulatory Requirements for Sensor Usage
Sensors deployed in various sectors, including healthcare, industrial automation, and environmental monitoring, are subject to specific regulatory frameworks. These regulations often address factors such as data accuracy, reporting procedures, and potential risks to public safety. Compliance with these regulations is essential to ensure legal operation and avoid potential penalties. For instance, medical sensors used in patient monitoring are subject to stringent guidelines regarding data privacy and security.
Safety Protocols for Handling and Using Various Sensors
Safe handling and use of sensors are crucial. The following table Artikels general safety protocols for different sensor types. Adherence to these protocols minimizes potential hazards and protects personnel.
Sensor Type | Safety Protocol |
---|---|
Pressure Sensors (Industrial) | Use appropriate personal protective equipment (PPE) like safety glasses and gloves. Regularly inspect pressure lines and valves for leaks or damage. Ensure proper grounding and electrical safety procedures. |
Chemical Sensors (Environmental) | Utilize appropriate ventilation systems and wear respirators when necessary. Follow manufacturer’s instructions carefully. Store and handle hazardous chemicals according to established procedures. |
Temperature Sensors (Food Processing) | Calibrate sensors regularly. Ensure proper insulation and temperature controls to prevent burns or freezing. Use sensor probes that are compatible with the materials being monitored. |
Motion Sensors (Security) | Ensure sensors are installed and maintained properly. Verify that the sensor’s field of view and sensitivity are adequate for the intended purpose. Consider potential interference from external factors. |
Legal Considerations in Public Space Deployments
Deploying sensor systems in public spaces raises legal concerns. Privacy issues and potential misuse of data collected by sensors need careful consideration. Compliance with data protection laws and regulations is paramount. For example, deploying facial recognition sensors in public spaces requires thorough legal review to ensure compliance with privacy regulations. Clear guidelines on data collection, storage, and usage should be established to avoid potential legal challenges.
Furthermore, the potential for sensor malfunction or error must be considered to avoid legal implications. For instance, malfunctioning traffic sensors could lead to accidents if their data is not processed accurately and used for real-time traffic management.
Ending Remarks
In conclusion, sensors are integral to modern advancements, influencing everything from healthcare to transportation. This exploration of sensor technology reveals the sophisticated processes involved in their creation, calibration, and integration into complex systems. Understanding these details empowers informed decision-making and opens doors to further innovation in diverse fields.
Top FAQs
What are some common sensor failure modes?
Common sensor failure modes include drift (gradual change in output), hysteresis (different outputs for the same input depending on direction), and saturation (failure to respond to further increases in input). Environmental factors like temperature and humidity can also affect sensor performance.
How do I choose the right sensor for a specific application?
Choosing the appropriate sensor depends on factors like the measured physical quantity, required accuracy, operating environment, cost, and size constraints. Consider the specific range of values to be measured and the desired response time.
What are the ethical considerations related to sensor technology?
Ethical considerations in sensor technology involve issues like data privacy, potential misuse of data, and the impact of sensor-driven decision-making on individuals and society. Ensuring responsible development and deployment of sensor systems is crucial.