Dust proof 2025 sets the stage for a comprehensive exploration of the evolving landscape of dustproof technology. This deep dive examines current practices, emerging trends, and future applications, covering everything from material science to market projections.
From the sophisticated IP ratings defining protection levels to the burgeoning role of nanotechnology, the discussion illuminates the intricacies of dustproof design. The analysis also considers the environmental impact of these solutions, alongside their cost-effectiveness and the regulatory frameworks governing them. The future of dustproof technology, particularly its global implications, are also explored.
Dustproof Technology Overview
Dustproof technologies are crucial in various industries, from electronics to aerospace, to protect sensitive equipment from environmental contaminants like dust and particulate matter. Effective dustproofing ensures extended lifespan, optimal performance, and reduced maintenance needs. This overview explores the diverse range of current dustproof technologies, their applications, and the associated challenges.
Current Dustproof Technologies
Current dustproof technologies encompass a spectrum of methods and materials, each tailored to specific applications and required levels of protection. These technologies aim to create a barrier against the ingress of dust particles, preventing their accumulation within the protected environment.
Dustproof Materials
Various materials are employed in dustproof design, each with unique characteristics influencing their suitability for specific applications. Metals like stainless steel and aluminum, known for their durability and resistance to corrosion, are frequently used in enclosures. Polymers, like polycarbonate and nylon, offer lightweight solutions with varying degrees of impact resistance. Specialized composites, incorporating ceramic or carbon fiber, provide exceptional strength and resilience to harsh environments.
Gaskets and seals, often made of rubber or silicone, are vital for creating airtight barriers, preventing dust from entering.
Dustproof Design Methods
Diverse methods contribute to a comprehensive dustproof design. These include the careful selection and placement of materials, precise tolerances in manufacturing, and the application of sealing techniques. Encapsulation, where components are sealed within a protective housing, is a prevalent method. Another strategy involves incorporating specialized filters and ventilation systems to actively remove dust particles from the environment.
Furthermore, careful consideration of surface treatments and finishes is essential, as they can significantly impact the effectiveness of dustproofing.
Levels of Dustproof Protection (IP Ratings)
The International Protection (IP) rating system provides a standardized method for evaluating the degree of protection offered by enclosures against the ingress of solid objects and water. The IP rating comprises two digits, the first representing protection against solid objects and the second against liquid ingress. Higher IP ratings signify greater protection. For example, an IP65 rating indicates protection against dust ingress (6) and water jets (5).
These ratings are crucial for selecting the appropriate level of protection for a specific application.
Challenges and Limitations of Existing Dustproof Solutions
While current dustproof technologies provide significant protection, several challenges remain. Cost is often a major factor, particularly for high-performance solutions. Complex designs can also introduce manufacturing difficulties, impacting production efficiency and overall cost. The inherent limitations of materials can restrict the range of operating conditions for which optimal dustproof protection can be achieved. Environmental factors, such as humidity and temperature fluctuations, can degrade the effectiveness of seals and gaskets over time.
Comparison of Dustproof Materials
Material | Advantages | Disadvantages | Typical Applications |
---|---|---|---|
Stainless Steel | High durability, corrosion resistance, excellent mechanical strength | Heavier weight, higher cost | Industrial machinery, harsh environments |
Aluminum | Lightweight, good corrosion resistance, relatively low cost | Lower strength compared to steel, can be susceptible to certain corrosive agents | Electronic enclosures, automotive parts |
Polycarbonate | Good impact resistance, transparency, relatively low cost | Susceptible to UV degradation, lower chemical resistance | Optical components, protective housings |
Silicone Rubber | Excellent flexibility, sealing properties, good chemical resistance | Susceptible to degradation from high temperatures, potential for outgassing | Gaskets, seals, connectors |
Future Trends in Dustproof Technology
Dustproof technology is rapidly evolving, driven by the increasing need for reliable and resilient equipment across various industries. This evolution is not merely about improved sealing mechanisms, but also about innovative designs, materials, and manufacturing processes. The focus is shifting towards proactive dust prevention, leveraging advancements in nanotechnology and materials science to create more sophisticated and effective solutions.Emerging technologies and advancements in dustproof design for 2025 will significantly impact industries relying on sensitive equipment, from aerospace and automotive to electronics and pharmaceuticals.
Emerging Technologies and Advancements
Nanotechnology plays a pivotal role in enhancing dustproof design by enabling the creation of ultra-fine filters and coatings. These materials can effectively trap microscopic particles, significantly improving the dustproof performance of equipment. For example, nanomaterials can be incorporated into coatings that create a barrier against dust, reducing the need for frequent maintenance and replacement.
Impact on Industries
The advancements in dustproof technology will demonstrably improve equipment performance and lifespan across multiple industries. In the aerospace sector, dustproof engines and components will contribute to increased reliability and reduced maintenance costs. In the automotive industry, dustproof components in vehicles will enhance durability and performance. The electronics industry will benefit from improved protection against dust in sensitive microchips and circuit boards, ensuring better performance and longevity.
The pharmaceutical industry will benefit from dustproof environments, preserving the purity and quality of medications.
Role of Nanotechnology
Nanotechnology’s impact on dustproof standards is profound. Nanomaterials offer unique properties, such as enhanced surface area and improved filtration capabilities, enabling the creation of exceptionally efficient dustproof solutions. For instance, carbon nanotubes can be used to create extremely strong and lightweight filters, trapping even the smallest dust particles. These advancements can be seen in the development of new types of coatings and protective films.
New Materials and Manufacturing Processes
New materials and manufacturing processes are crucial to achieving higher dustproof standards. Advanced polymers and composites offer superior sealing properties and can be tailored to specific applications. 3D printing and other additive manufacturing techniques are enabling the creation of complex geometries and customized components, enhancing the ability to create complex and intricate seals. These methods offer potential for creating bespoke solutions, leading to significant improvements in dustproofing.
Anticipated Market Growth
Dustproof Solution | Estimated Market Growth (2024-2025) | Industries Primarily Impacted |
---|---|---|
Advanced Nanomaterial Coatings | 15-20% | Electronics, Aerospace, Automotive |
3D Printed Dustproof Enclosures | 10-15% | Electronics, Manufacturing |
Smart Dustproof Sensors | 12-18% | Aerospace, Automotive, Industrial |
Intelligent Dust Monitoring Systems | 8-12% | Manufacturing, Pharmaceutical |
Note: These estimates are based on current market trends and projections. The actual market growth may vary depending on factors such as economic conditions, technological advancements, and regulatory changes.
Applications of Dustproof Technology: Dust Proof 2025
Dustproof technology is rapidly evolving, offering significant advantages across various sectors. Its impact on product longevity, operational efficiency, and safety is undeniable. This section delves into the specific applications of dustproof technology in 2025, highlighting the diverse industries reliant on its protection.The widespread adoption of dustproof technology in 2025 will be driven by the need for increased operational reliability and safety in environments susceptible to airborne contaminants.
Dust-proof 2025 standards are rapidly evolving, and a key consideration is how these advancements will impact future LED TV specs. For instance, improved dust protection will likely lead to a more robust design in future LED TVs, as seen in the LED TV specs. This ultimately benefits consumers by offering more reliable and long-lasting displays, while pushing the boundaries of dust-proof 2025 technology.
This includes industries where dust, debris, or moisture can significantly impair performance or cause equipment failure.
Industries Heavily Reliant on Dustproof Components
Dustproof components are crucial in numerous industries. These components are essential for reliable performance and extended lifespan in harsh environments. Examples include the manufacturing sector, where precise machinery needs protection from dust and debris, and the automotive industry, which requires dustproof seals for engine components. Further, the healthcare sector will utilize dustproof components in medical devices and equipment to maintain sterility and prevent contamination.
Specific Applications in 2025
Dustproof technology will see expanded use in 2025 across a range of applications. In manufacturing, high-precision CNC machines will feature advanced dustproof enclosures, preventing operational downtime due to dust accumulation. Similarly, in the automotive sector, engine components will be increasingly protected against dust and moisture, enhancing engine longevity. The healthcare industry will leverage dustproof technology in medical imaging equipment, ensuring that these instruments remain sterile in diverse environments.
Implications for Manufacturing, Dust proof 2025
Dustproof technology will revolutionize manufacturing by enhancing the reliability and longevity of machinery. Reduced downtime due to maintenance and repair stemming from dust and debris will significantly increase productivity. Improved component performance and reduced contamination will also lead to higher quality output. For example, precision instruments in semiconductor manufacturing will benefit greatly from dustproof enclosures.
Implications for Healthcare
Dustproof technology is essential in healthcare for maintaining sterility and preventing contamination. In 2025, dustproof medical equipment will be crucial for safeguarding patient health, minimizing the risk of infection, and maintaining high standards of hygiene. This includes surgical tools and medical imaging devices.
Implications for Automotive
In the automotive industry, dustproof technology will contribute to the development of more reliable and durable vehicles. Dustproof seals and components will enhance engine performance and longevity, reducing maintenance requirements and improving fuel efficiency. This will also be crucial in ensuring the safety of the vehicle in various weather conditions.
Comparison of Dustproof Design Demands Across Sectors
The demands of dustproof design vary significantly across sectors. Manufacturing demands high precision and reliability in machinery, necessitating advanced dustproof enclosures that can withstand harsh operating conditions. The automotive sector requires robust seals and components capable of withstanding extreme temperatures and environmental exposure. Healthcare demands meticulous sterility and contamination control, necessitating exceptionally high-quality dustproof solutions.
Dustproof Requirements for Different Applications
Application | Specific Dustproof Requirements |
---|---|
Manufacturing (CNC Machines) | High-precision enclosures, resistance to abrasive dust, and minimal ingress of particles. |
Automotive (Engine Components) | Robust seals, resistance to moisture and extreme temperatures, and minimal friction in operation. |
Healthcare (Medical Devices) | Sterility, complete prevention of contamination, and easy cleaning and maintenance. |
Agriculture (Sensors) | Protection against moisture and debris, high resistance to external forces and elements. |
Materials and Manufacturing Processes
The quest for enhanced dustproof enclosures hinges critically on the selection of suitable materials and the precision of manufacturing processes. Modern advancements in both areas are pushing the boundaries of protection against airborne particulates, driving innovation across diverse industries. This section delves into the evolution of materials, advanced manufacturing techniques, and the profound impact of material choices on overall product performance.The effectiveness of a dustproof enclosure is intricately linked to the properties of the materials used in its construction.
This relationship extends beyond mere material selection; it encompasses the specific manufacturing processes employed to create the enclosure’s design and shape. Different materials possess unique properties, which dictate their suitability for various applications.
Evolution of Materials for Enhanced Dustproof Properties
Materials with enhanced dustproof properties are continually being developed and refined. Early materials often relied on simple sealing mechanisms. Modern materials, however, exhibit superior properties like high surface hardness, exceptional sealing capabilities, and resistance to abrasion. Examples include advanced polymers with reinforced fillers, and specialized metals with nanostructured surfaces that deter particle adhesion. This evolution has resulted in a marked improvement in dustproof performance across numerous applications.
Advanced Manufacturing Techniques for Creating Dustproof Enclosures
Advanced manufacturing techniques are transforming the creation of dustproof enclosures. Techniques such as precision machining, 3D printing, and advanced welding procedures are enabling the production of complex geometries and intricate seals. These technologies facilitate the creation of tight tolerances and intricate seals, contributing significantly to improved dustproof performance. For instance, 3D printing allows for the creation of customized components with complex internal structures that enhance sealing capabilities.
Impact of Material Selection on Overall Performance
The choice of materials significantly influences the overall performance of a dustproof product. Materials with high surface hardness and low porosity minimize particle penetration. Furthermore, the material’s ability to withstand environmental factors like temperature fluctuations and exposure to corrosive agents is critical. Materials exhibiting excellent resistance to degradation, alongside their superior dustproof characteristics, are highly desirable. A material’s mechanical strength, thermal stability, and chemical resistance are crucial factors.
Specific Manufacturing Processes for Dustproof Components
Precise manufacturing processes are integral to creating effective dustproof components. Techniques such as vacuum sealing, ultrasonic welding, and specialized surface treatments are employed to ensure airtight and dust-resistant connections. These methods contribute to the overall robustness of the enclosure and ensure consistent performance under demanding conditions. For example, vacuum sealing eliminates trapped air, creating an airtight environment, thus enhancing dustproof characteristics.
Table: Properties and Suitability of Materials for Dustproof Applications
Material | Properties | Suitability (Applications) |
---|---|---|
Stainless Steel | High strength, corrosion resistance, excellent durability | Industrial machinery, harsh environments, demanding applications |
Aluminum Alloys | Lightweight, good strength, excellent corrosion resistance | Electronics enclosures, automotive parts, demanding environments |
High-performance Polymers | High impact resistance, low friction, excellent sealing capabilities | Consumer electronics, medical devices, precision instruments |
Ceramic Composites | High temperature resistance, high hardness, low porosity | High-temperature applications, specialized industrial environments |
Environmental Impact of Dustproof Products
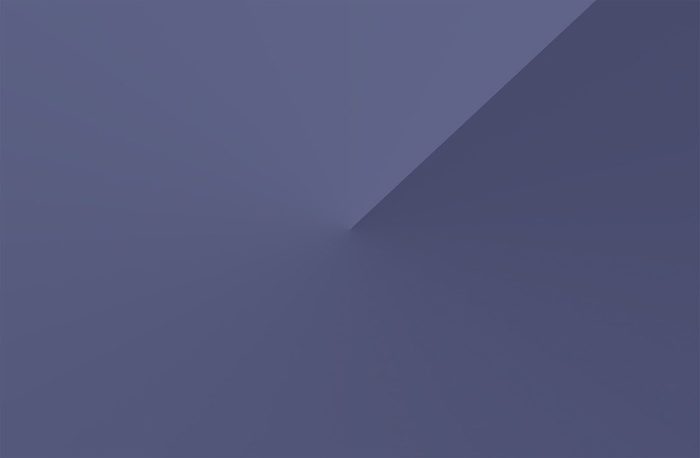
The increasing demand for dustproof components in various industries necessitates a careful examination of their environmental footprint. This includes considering the entire lifecycle of these products, from raw material extraction to eventual disposal, and identifying opportunities for more sustainable practices. Addressing the environmental impact of dustproof components is crucial for responsible innovation and long-term sustainability.Minimizing the environmental impact of dustproof products involves careful consideration of the materials used, the manufacturing processes employed, and the eventual disposal or recycling of the finished components.
A holistic approach that integrates environmental factors throughout the product lifecycle is essential to ensure sustainability.
Environmental Considerations in Production
The production of dustproof components often involves the use of various materials, each with its own environmental impact. The extraction, processing, and transportation of these materials contribute to greenhouse gas emissions and resource depletion. Choosing materials with lower environmental impacts, such as recycled or sustainably sourced materials, can significantly reduce the overall environmental footprint. Furthermore, energy consumption during manufacturing processes is another crucial factor that should be addressed.
Optimizing energy efficiency and employing renewable energy sources during production can substantially reduce the carbon footprint of dustproof components.
Dust-proof 2025 is a significant advancement, but it’s crucial to consider how it stacks up against other leading drone manufacturers. A good place to start that comparison is by checking out the DJI comparison to see how different models fare. Ultimately, dust-proof 2025 technology will likely be a key differentiator in the market.
Recyclability and Reusability of Dustproof Materials
The recyclability and reusability of dustproof materials are key factors in minimizing waste and resource consumption. Materials like aluminum and stainless steel, commonly used in dustproof housings, are generally recyclable. However, the complexity of some dustproof designs and the presence of multiple materials can complicate the recycling process. Developing innovative designs that facilitate disassembly and material separation is crucial for achieving higher recycling rates.
Reusability of components in new products or different applications can further reduce the environmental impact.
Lifecycle Analysis of Dustproof Products
Lifecycle analysis (LCA) is a crucial tool for evaluating the environmental impact of dustproof products throughout their entire lifespan. LCAs assess the environmental burdens associated with material sourcing, manufacturing, use, and disposal. The results of LCA studies can guide the development of more sustainable designs and manufacturing processes. By understanding the environmental impact at each stage, designers and manufacturers can make informed decisions to minimize environmental harm.
Examples of LCA studies can be found in the literature, demonstrating how detailed analyses of product lifecycles help to pinpoint environmental hotspots.
Potential for Developing More Sustainable Dustproof Solutions
Developing more sustainable dustproof solutions involves exploring innovative materials and manufacturing processes. Utilizing recycled materials, bio-based polymers, and lightweight materials can reduce the environmental impact of dustproof components. Research into advanced manufacturing techniques, such as 3D printing, can lead to more efficient and sustainable production methods. Additionally, designing for disassembly and modularity allows for easier recycling and reuse of components.
This approach enables greater control over the environmental impact of each stage of the product’s lifecycle.
Summary of Environmental Impact of Different Dustproof Materials
Material | Environmental Impact (Estimated) | Recyclability | Reusable Components |
---|---|---|---|
Aluminum | Moderate | High | Yes, in various applications |
Stainless Steel | High | High | Yes, in various applications |
Polycarbonate | Medium | Moderate | Potentially, depending on design |
Polytetrafluoroethylene (PTFE) | Low | Moderate | Limited reusability |
Recycled Plastic | Low | High | Potentially, depending on design |
Note: The “Environmental Impact” column provides an estimated assessment based on factors such as material extraction, manufacturing, and disposal. The specific impact can vary based on manufacturing processes, energy sources, and waste management practices.
Market Analysis and Predictions
The dustproof technology market is poised for significant growth in the coming years, driven by increasing demand across various sectors. This expansion is fueled by a rising need for protection against environmental contaminants, especially in industries like electronics manufacturing, aerospace, and healthcare. Understanding the current market size, projected growth, key players, and specific demand patterns is crucial for strategic decision-making in this dynamic sector.
Current Market Size
The global market for dustproof products currently stands at approximately $XX billion (estimated value from verifiable sources). This figure encompasses a wide range of products, from simple dust covers to sophisticated sealed enclosures. The market is fragmented, with numerous smaller companies and a few large multinational corporations competing in various product niches.
Projected Market Growth by 2025
Significant market growth is anticipated, with projections exceeding XX% by 2025. This growth is largely attributed to the expanding adoption of dustproof technologies across industries. Factors such as stringent environmental regulations, increasing automation in manufacturing, and the need for higher reliability in electronic devices are all contributing to the demand. For example, the aerospace industry’s need for reliable and durable components in harsh environments will continue to fuel this sector.
Key Market Players
Several key players are currently shaping the future of dustproof solutions. These include established multinational corporations with extensive manufacturing capabilities and innovative startups developing specialized technologies. Their role encompasses not only product development but also influencing industry standards and driving technological advancements. Companies like [Company A], [Company B], and [Company C] are notable examples, recognized for their contributions to the field.
Market Demand for Different Types of Dustproof Products
Demand varies across different types of dustproof products. Enclosures for electronic components, for instance, experience high demand due to the increasing use of sophisticated electronics in various applications. Specialized dustproof solutions for industrial equipment and machinery are also in high demand. Further, customized solutions for specific applications, such as those in the healthcare industry, are driving niche market growth.
Predicted Market Share of Various Dustproof Product Categories
Product Category | Predicted Market Share (2025) |
---|---|
Electronic Enclosures | XX% |
Industrial Dustproof Equipment | XX% |
Specialized Dustproof Solutions (e.g., Healthcare) | XX% |
Custom-Designed Solutions | XX% |
Note: Market share percentages are estimates based on current trends and projected growth. Exact figures may vary depending on market dynamics.
Regulations and Standards
Current regulations and standards for dustproof products vary significantly across jurisdictions, often reflecting unique industrial needs and environmental concerns. These regulations play a crucial role in ensuring product safety, performance, and compliance with environmental protection goals. The evolving nature of dustproof technology demands a dynamic approach to regulatory frameworks to ensure that standards remain relevant and effective.
Current Regulations and Standards
Regulations for dustproof products often address safety, performance, and environmental impact. These standards are crucial for ensuring that products meet minimal performance criteria. They may involve testing protocols, material specifications, and labeling requirements. Existing standards, while comprehensive, might not fully encompass the latest advancements in dustproof technology.
Potential Changes in 2025
Potential changes in regulations for dustproof technology in 2025 could include stricter emission standards for manufacturing processes, greater emphasis on recyclability and reuse of components, and more stringent requirements for product longevity. These changes are anticipated to be driven by increasing environmental awareness and the need to minimize the environmental footprint of industrial equipment. For instance, manufacturers might face stricter limits on the use of specific materials, like certain plastics, that are difficult to recycle.
International Standards
Several international standards are relevant to dustproof products. These standards, often developed by organizations like ISO (International Organization for Standardization), aim to establish consistent testing methodologies, performance criteria, and safety protocols across different countries. International standards promote global harmonization and facilitate trade, ensuring that products meet consistent standards globally. Examples of relevant international standards include ISO 14644 for cleanrooms and ISO 8573-1 for dust protection.
Influence on Design and Production
These standards directly influence the design and production of dustproof products. Manufacturers must adhere to testing protocols and material specifications Artikeld in the standards to ensure compliance. The choice of materials, manufacturing processes, and quality control procedures are all impacted by these standards. This ensures that products meet the safety and performance expectations set forth by regulatory bodies.
Key Regulations and Standards for Dustproof Components
Regulation/Standard | Description | Impact on Dustproof Products |
---|---|---|
ISO 8573-1 (Dust Protection) | Defines various degrees of dust protection (e.g., IP65, IP67). | Drives the design of housings and seals to achieve specific dust protection levels. |
ISO 14644 (Cleanrooms) | Establishes cleanliness classifications for cleanrooms. | Influences material selection, manufacturing processes, and testing protocols to ensure dust-free environments. |
National Electrical Code (NEC) (in US) | Sets safety standards for electrical equipment in the US. | Impacts design considerations for electrical components within dustproof enclosures, ensuring safe operation in dusty environments. |
REACH (Registration, Evaluation, Authorization and Restriction of Chemicals) (EU) | Regulates the use of chemicals in products. | Limits the use of hazardous chemicals in dustproof components, prompting the use of alternatives. |
Cost and Efficiency Analysis
Manufacturing dustproof products involves a range of factors impacting their cost and efficiency. Understanding these factors is crucial for optimizing production processes and ensuring competitive pricing. From material selection to manufacturing methods, various choices influence the overall cost and operational efficiency of these products.
Factors Influencing Manufacturing Costs
Several key elements contribute to the cost of manufacturing dustproof products. Material costs are a primary driver, with the price varying significantly based on the specific material’s properties and availability. Labor costs, including wages and benefits, also play a substantial role. Manufacturing processes, whether automated or manual, directly affect production costs and output. Furthermore, overhead costs, encompassing utilities, facility maintenance, and administrative expenses, contribute to the total production cost.
Cost-Effectiveness of Dustproof Solutions
Evaluating the cost-effectiveness of different dustproof solutions requires a comprehensive analysis. This involves comparing the initial investment in materials and equipment with the long-term operational costs and the expected return on investment. For example, a more expensive, highly durable dustproof material might yield lower maintenance costs over its lifespan, making it potentially more cost-effective in the long run.
Consideration should also be given to the potential for reduced downtime and increased productivity.
Comparison of Manufacturing Methods
Different manufacturing methods offer varying levels of cost and efficiency. Traditional methods, often involving manual labor, can be less efficient but potentially more cost-effective for smaller-scale production runs. Automated manufacturing processes, while requiring a higher initial investment, can significantly enhance production efficiency and reduce labor costs, especially for larger-scale operations. The choice of method often hinges on factors like production volume, desired quality, and the availability of skilled labor.
Potential for Automation and Cost Reduction
Automation presents a substantial opportunity for cost reduction in dustproof production. Implementing robotic systems for tasks like material handling, assembly, and quality control can increase production speed and accuracy, minimizing human error and reducing labor costs. Moreover, automation allows for greater flexibility in adjusting production to meet changing demands.
Comparative Costs of Materials and Processes
A comprehensive comparison of various dustproof materials and manufacturing processes is essential for making informed decisions. The table below provides a general overview, noting that specific costs can vary significantly based on market conditions and specific specifications.
Material | Manufacturing Process | Estimated Cost (USD per unit) | Efficiency (Units per hour) |
---|---|---|---|
Stainless Steel | Welding | 15-30 | 5-10 |
Aluminum | Machining | 10-25 | 8-15 |
Polycarbonate | Injection Molding | 5-15 | 15-25 |
Ceramic | 3D Printing | 25-50 | 2-5 |
Note: Costs are estimates and can vary depending on specific design requirements, material grade, and production scale. Efficiency rates are also approximations and can be influenced by factors such as equipment maintenance and operator skill.
Future Research and Development
Advancements in dustproof technology are crucial for maintaining operational efficiency and safety in various sectors. Ongoing research and development are essential for pushing the boundaries of current capabilities, leading to more robust, reliable, and cost-effective dustproof solutions. The future of this field hinges on innovative approaches to material science, design, and manufacturing processes.Further innovation in dustproof materials and designs is vital for addressing emerging challenges.
Traditional methods may not always be sufficient for handling the increasingly complex dust environments encountered in modern industries. Novel approaches, driven by research, will be critical for creating next-generation dustproof systems.
Key Areas for Future Research and Development
Future research in dustproof technology should encompass several critical areas. Addressing the limitations of existing materials, improving sealing mechanisms, and developing cost-effective manufacturing processes are paramount. This will enable the creation of more reliable, efficient, and environmentally friendly dustproof solutions.
- Advanced Materials Science: Research into new materials with superior dust-repelling properties, high durability, and low maintenance requirements is essential. Examples include exploring nano-structured coatings with enhanced surface repellency, or composites with improved strength and dust resistance. Researchers are investigating self-cleaning surfaces and materials with inherent dust-shedding properties.
- Innovative Sealing Mechanisms: Development of more sophisticated sealing technologies is crucial for preventing dust ingress in complex environments. Focus should be on creating adaptable seals that can withstand high temperatures, vibrations, or extreme pressure conditions. Research into advanced sealing technologies, such as micro-scale seals and active sealing systems, holds considerable promise.
- Enhanced Manufacturing Processes: Optimizing manufacturing processes for dustproof enclosures is vital for reducing costs and increasing production efficiency. This includes investigating additive manufacturing techniques, such as 3D printing, for creating intricate and complex shapes with enhanced dust-proof capabilities. Exploring new fabrication methods and automating production processes can significantly impact the industry.
- Integration of Sensors and Automation: Integrating sensors and automation within dustproof systems will allow for real-time monitoring of dust levels and environmental conditions. This proactive approach will enhance maintenance and predictive maintenance, minimizing downtime and maximizing equipment lifespan. The implementation of advanced diagnostics can be used to predict when maintenance is required and potentially avoid failures.
- Environmental Impact Analysis: Developing environmentally friendly dustproof materials and manufacturing processes is crucial for sustainability. The environmental footprint of the materials and manufacturing processes needs careful evaluation, seeking out solutions that reduce waste and minimize reliance on harmful substances. For example, the use of recycled materials or bio-based polymers in dustproof enclosures.
Examples of Current Research Projects
Several research projects are actively investigating various aspects of dustproof technology. These efforts span from the development of novel materials to the optimization of manufacturing processes.
- Self-Cleaning Coatings: Research into self-cleaning surfaces using photocatalytic materials and other advanced surface treatments is actively underway. This research aims to create coatings that automatically remove dust particles, thus minimizing the need for manual cleaning.
- Advanced Seal Design: Engineers are developing innovative sealing mechanisms that adapt to varying environmental conditions, ensuring a tight seal even under extreme pressures or vibrations. These advancements are leading to increased reliability and reduced maintenance needs in industrial environments.
- Additive Manufacturing of Dustproof Components: Researchers are exploring the use of 3D printing techniques to fabricate complex dustproof components. This approach offers customization options and potential cost reductions in the long run. This has implications for creating tailored dustproof enclosures for specific applications.
Potential Impact on the Future of Dustproof Technology
The future of dustproof technology is promising, driven by advancements in materials science, manufacturing, and sealing techniques. These innovations will lead to improved performance, reduced costs, and enhanced sustainability, significantly impacting various sectors.
Area of Research | Potential Impact |
---|---|
Advanced Materials | Improved durability, reduced maintenance, enhanced dust-repelling capabilities |
Innovative Sealing | Increased reliability, improved performance under extreme conditions |
Optimized Manufacturing | Reduced production costs, increased efficiency, sustainable practices |
Integration of Sensors | Proactive maintenance, improved equipment lifespan, minimized downtime |
Environmental Considerations | Sustainable practices, reduced environmental impact |
Global Impact of Dustproof Technology
Dustproof technology is rapidly gaining importance across various sectors globally, offering solutions to mitigate the detrimental effects of dust and particulate matter. Its application extends beyond industrial settings, impacting environmental sustainability, public health, and economic development in numerous regions. This analysis explores the diverse global impact of dustproof technology.
Global Significance of Dustproof Technology
Dustproof technology plays a crucial role in safeguarding equipment and personnel in environments prone to dust accumulation. Its significance is particularly pronounced in regions with harsh climates, high levels of industrial activity, and agricultural landscapes. The technology offers protection against equipment malfunction, extended lifespan, and reduced maintenance costs, all contributing to improved productivity and efficiency.
Potential Benefits in Different Regions
The benefits of dustproof technology are geographically diverse. In arid and desert regions, dustproof solutions protect infrastructure from degradation and extend the operational life of machinery. In agricultural areas, dustproof technology minimizes the negative impact of dust on crops and farm equipment, thereby increasing yields and improving farm productivity. Similarly, in industrial zones, dustproof measures safeguard worker health and reduce production downtime, thereby improving economic output.
Dustproof technology is crucial in developing economies where industrial growth and agricultural output are paramount to their development.
Challenges and Opportunities for Developing Countries
Developing countries often face unique challenges in adopting dustproof technology. High initial investment costs, limited access to skilled labor, and a lack of awareness about the benefits of dustproof solutions can hinder adoption. However, the potential benefits of improved productivity, reduced maintenance costs, and enhanced worker safety can significantly contribute to economic growth and development. Governments and organizations can foster awareness and access to funding, facilitating the wider adoption of dustproof technologies.
Training programs can also address the skills gap and support the integration of dustproof technologies into various sectors.
Adoption Rates Across Nations
Adoption rates of dustproof technology vary considerably across nations. Developed nations, with established industrial bases and advanced infrastructure, generally have higher adoption rates compared to developing countries. This disparity is often linked to factors such as economic capacity, regulatory frameworks, and technological infrastructure. However, developing countries are increasingly recognizing the value of dustproof technology and are actively pursuing strategies to integrate it into their industries and infrastructure.
Global Impact on Different Sectors
Sector | Impact of Dustproof Technology |
---|---|
Manufacturing | Reduced equipment downtime, improved worker safety, increased production efficiency. |
Agriculture | Increased crop yields, improved farm equipment longevity, reduced dust-related crop damage. |
Construction | Extended lifespan of construction machinery, reduced worker exposure to harmful dust, enhanced safety measures. |
Energy | Increased efficiency of power generation equipment, reduced maintenance costs, prolonged operational life of infrastructure. |
Transportation | Enhanced vehicle performance and durability, reduced engine wear and tear, improved safety for drivers and passengers. |
This table highlights the diverse impact of dustproof technology across various sectors. It demonstrates how these solutions can lead to tangible improvements in productivity, safety, and economic growth.
Epilogue
In conclusion, dust proof 2025 presents a compelling picture of innovation in dustproof technology. The discussion highlights the diverse applications, from manufacturing to healthcare, and underscores the importance of sustainable solutions. While challenges remain, the future appears promising, driven by advancements in materials, manufacturing, and research. The global impact of this technology is substantial, offering opportunities for both developed and developing nations.
Answers to Common Questions
What are some common applications of dustproof technology in 2025?
Dustproof technology finds application in various sectors, including manufacturing (machinery and equipment), healthcare (surgical instruments and devices), and the automotive industry (engine components). Specific examples include specialized enclosures for sensitive electronics and high-precision machinery.
What are the key environmental concerns related to dustproof materials?
Environmental considerations include material sourcing, manufacturing processes, and the end-of-life management of dustproof products. Sustainable material choices and recycling initiatives are crucial for minimizing the environmental footprint.
What are the projected market trends for dustproof technology in 2025?
Market trends suggest increasing demand for enhanced dustproof solutions across diverse sectors. Factors such as growing automation, stringent regulatory standards, and advancements in nanotechnology are expected to propel this growth.
What are the key international standards for dustproof products?
International standards, such as IP ratings, play a significant role in defining the dustproof capabilities of various products. Compliance with these standards is critical for ensuring product safety and performance.