Magnetic connector 2025 sets the stage for a fascinating exploration of this rapidly evolving technology. This detailed analysis delves into the market, technological advancements, design considerations, manufacturing processes, applications across various industries, standards, future trends, cost analysis, and supply chain implications.
The report anticipates substantial growth in the magnetic connector market by 2025, fueled by technological advancements and increasing demand in sectors like consumer electronics, automotive, and industrial automation. Key segments and applications will be highlighted, along with a critical examination of the design, manufacturing, and cost considerations that will impact this burgeoning industry.
Market Overview
The magnetic connector market is poised for significant growth in 2025, driven by increasing demand across diverse industries. This expansion is fueled by the inherent advantages of magnetic connectors, including their lightweight design, quick assembly, and reduced wiring complexity. These factors are particularly attractive in applications requiring portability, ease of maintenance, and rapid prototyping.Technological advancements are continuously refining magnetic connector design, leading to improved performance and wider applicability.
This is further enhanced by the growing need for miniaturization and higher data transfer rates in electronic devices. This evolution is expected to significantly impact various sectors, from consumer electronics to industrial automation.
Projected Growth and Market Size Estimations
The magnetic connector market is anticipated to experience substantial growth in 2025. Projected growth rates vary across different segments, influenced by factors such as technological innovation, industrial trends, and consumer preferences. Reliable market research indicates a positive trajectory, with estimations suggesting a substantial increase in market size compared to previous years. For instance, the automotive sector is projected to witness a notable surge in the adoption of magnetic connectors due to their suitability for complex wiring harnesses.
Key Market Segments
Several key segments contribute to the magnetic connector market. These segments include consumer electronics, industrial automation, automotive, and medical devices. Each segment presents unique challenges and opportunities for magnetic connector manufacturers, demanding specialized designs and manufacturing processes. For example, consumer electronics often prioritize miniaturization and aesthetics, while industrial automation emphasizes robustness and reliability.
Potential Applications
Magnetic connectors offer a wide range of applications across diverse industries. These include but are not limited to:
- Consumer Electronics: Portable devices, such as laptops and smartphones, benefit from magnetic connectors’ ease of assembly and disassembly.
- Industrial Automation: Robotic systems and machinery often employ magnetic connectors for rapid connection and disconnection of components.
- Automotive: Wiring harnesses in vehicles can leverage magnetic connectors to reduce assembly time and improve the safety and reliability of connections.
- Medical Devices: Medical instruments and equipment can utilize magnetic connectors for sterile assembly and easy maintenance.
The versatility of magnetic connectors allows for adaptability across numerous applications, showcasing their potential to revolutionize various industries.
Technological Advancements
Technological advancements in magnetic connector design are crucial to their widespread adoption. This includes improvements in materials, such as higher strength and corrosion resistance alloys, leading to enhanced durability and performance. Miniaturization is another critical aspect, with designs continuously evolving to fit smaller spaces and meet the demands of compact devices. Moreover, enhanced data transfer capabilities are being integrated into magnetic connectors, ensuring compatibility with advanced communication protocols.
Magnetic connectors are predicted to be crucial for 2025’s portable home automation devices. These compact, versatile components will likely play a key role in the design and functionality of portable home automation systems, facilitating seamless integration and reducing complexity. Their lightweight and robust nature will be a definite advantage for future iterations of magnetic connector 2025.
Market Segmentation Analysis
Segment | Projected Growth | Applications |
---|---|---|
Consumer Electronics | Moderate to High | Smartphones, laptops, wearables |
Industrial Automation | High | Robotics, machinery, manufacturing equipment |
Automotive | High | Wiring harnesses, sensors, actuators |
Medical Devices | Moderate | Surgical instruments, diagnostic equipment |
The table highlights the diverse applications and expected growth projections for each segment within the magnetic connector market. This comprehensive overview provides a clear understanding of the industry’s potential for growth and innovation in 2025.
Technological Advancements
Magnetic connectors are experiencing a surge in innovation, driven by the need for smaller, faster, and more reliable interconnections in various sectors. This evolution is propelling advancements in materials science, manufacturing techniques, and performance characteristics, all contributing to the broader trend of miniaturization. The improved performance characteristics are crucial for the seamless integration of magnetic connectors into emerging technologies.
Latest Innovations in Magnetic Connector Technology
The field of magnetic connectors is witnessing significant advancements, including the development of novel magnetic materials with enhanced performance characteristics. Researchers are exploring new alloys and composite materials to achieve higher magnetic flux densities, improved energy efficiency, and enhanced durability. These innovations promise to revolutionize the performance of magnetic connectors, leading to increased efficiency and reliability in various applications.
Emerging Materials and Manufacturing Processes
A key area of advancement lies in the development of advanced materials. Rare-earth magnets, such as neodymium-iron-boron (NdFeB), continue to be a cornerstone, but researchers are exploring alternative, potentially more sustainable, materials like ferrite magnets or combinations of different materials. New manufacturing processes are also being implemented to create more complex geometries and intricate designs in magnetic connectors.
Additive manufacturing (3D printing) is emerging as a powerful tool, allowing for the creation of customized parts with intricate features and potentially reduced manufacturing costs. Micro-fabrication techniques are being used to create highly precise and miniaturized magnetic connector components, further enabling their use in compact devices.
Improved Performance Characteristics of 2025 Magnetic Connectors
The performance characteristics of 2025 magnetic connectors are expected to exhibit significant improvements. Increased magnetic force will allow for more compact designs while maintaining high reliability. Enhanced corrosion resistance will be critical for outdoor applications and demanding environments. Faster connection/disconnection cycles, reduced contact resistance, and improved power handling capabilities are also anticipated. The miniaturization trend will lead to even faster switching times and improved overall performance.
Magnetic connector 2025 is poised for some serious advancements, potentially revolutionizing the industry. A key factor in this evolution is the development of faster RAM, like the RAM 2025 RAM 2025 , which will directly impact the speed and efficiency of these connectors. Ultimately, this all translates to better performance for magnetic connectors in 2025.
Significance of Miniaturization in Magnetic Connector Design
Miniaturization is a critical driver in the design of magnetic connectors. The trend towards smaller, more portable electronic devices necessitates the creation of miniature connectors. This demands highly efficient magnetic fields within compact volumes. Miniaturization leads to lighter weight devices, increased power density, and improved energy efficiency. Miniaturization is also critical for the integration of magnetic connectors into new technologies.
Examples of Enhancing Existing Technologies
Magnetic connectors are enhancing existing technologies in diverse ways. In wearable electronics, they enable flexible and adaptable designs. In automotive applications, they offer a solution for robust and secure connections in harsh environments. The integration of magnetic connectors in industrial automation allows for modularity and dynamic reconfiguration of assembly lines. The miniaturization of these connectors is also revolutionizing medical device technology.
Table of Material Properties, Manufacturing Processes, and Performance Metrics
Material | Manufacturing Process | Magnetic Force (N) | Operating Temperature (°C) | Corrosion Resistance | Cycle Life (connections) |
---|---|---|---|---|---|
NdFeB | Injection Molding | 1.5-2.0 | -40 to +85 | Good | >10,000 |
Ferrite | Powder Metallurgy | 0.8-1.2 | -55 to +125 | Excellent | >20,000 |
Composite | 3D Printing | 1.0-1.5 | -20 to +100 | Good | >5,000 |
Note: Values are approximate and can vary depending on specific material composition and design.
Design Considerations
Designing magnetic connectors for 2025 necessitates careful consideration of various factors to ensure high performance, reliability, and cost-effectiveness. A comprehensive approach encompassing design variations, durability, thermal management, and packing density is crucial for success in the evolving market. The increasing demand for miniaturization and higher data transfer rates requires innovative designs that meet these stringent requirements.The efficacy of a magnetic connector hinges on its ability to withstand the rigors of operation while maintaining stable performance.
This includes robustness against mechanical stress, environmental conditions, and thermal fluctuations. Optimization in these areas is paramount to achieving a product that is reliable and durable in the long term.
Comparison of Magnetic Connector Designs
Different magnetic connector designs offer varying advantages and disadvantages. Understanding these nuances is critical for selecting the most appropriate design for a given application. Consideration of the specific application requirements and constraints is vital. A thorough evaluation of the pros and cons of each design is necessary for informed decision-making.
- Surface-mounted connectors: These connectors are often smaller and lighter than their through-hole counterparts. Their flat profile facilitates easier integration into compact devices, but they might have limitations in terms of the amount of current they can handle.
- Through-hole connectors: These connectors, often used in larger applications, offer greater current-carrying capacity and robust mechanical strength. However, their larger size may not be suitable for all applications requiring compactness.
- Array connectors: These connectors utilize multiple magnetic elements to facilitate higher current density. They are often found in applications demanding high data transfer rates. Potential challenges include maintaining alignment accuracy across multiple elements.
Reliability and Durability
Ensuring the reliability and durability of magnetic connectors is paramount for long-term performance. This requires careful material selection, robust manufacturing processes, and rigorous testing protocols.
- Material selection: Choosing materials with high resistance to corrosion, fatigue, and wear is crucial for long-term reliability. The selection must also account for the operating environment.
- Manufacturing processes: Stringent manufacturing standards ensure precise tolerances and consistent quality. This reduces the likelihood of component failure and improves overall connector lifespan.
- Testing protocols: Rigorous testing under various environmental conditions (temperature, vibration, shock) is essential to validate the connector’s durability and reliability. These tests should emulate real-world operating conditions.
Thermal Management
Effective thermal management is essential to prevent overheating, which can compromise connector performance and lifespan. Heat dissipation strategies are crucial for maintaining stable operating conditions.
- Thermal conductive materials: Integrating thermal conductive materials in the connector design can effectively dissipate heat generated during operation.
- Heat sinks: Implementing heat sinks can further enhance heat dissipation and maintain optimal operating temperatures.
- Active cooling: In high-power applications, active cooling solutions might be necessary to manage the heat generated by the connector.
High-Density Packing
Achieving high-density packing in magnetic connectors is a critical aspect for miniaturization. Optimizing the arrangement and spacing of magnetic elements is key.
- Optimized element arrangement: Careful arrangement of magnetic elements can maximize space utilization and reduce the overall size of the connector.
- Minimizing air gaps: Minimizing air gaps between magnetic elements is essential to enhance the magnetic field strength and maintain connection integrity.
- Advanced material properties: Utilizing materials with improved magnetic properties, such as higher permeability, can contribute to achieving high-density packing.
Critical Design Parameters
A comprehensive list of critical parameters for magnetic connector design includes:
- Magnetic field strength: The strength of the magnetic field is critical for proper connection.
- Operating temperature range: The temperature range within which the connector can operate reliably.
- Current carrying capacity: The maximum current the connector can safely handle.
- Mechanical strength: The ability of the connector to withstand various mechanical stresses.
- Connector size: The physical dimensions of the connector are important for compatibility and integration into devices.
Comparison Table of Connector Designs
Connector Design | Advantages | Disadvantages |
---|---|---|
Surface-mounted | Compact size, lightweight | Limited current handling capacity |
Through-hole | High current carrying capacity, robust | Larger size, increased space requirements |
Array | High current density, high data transfer rates | Alignment accuracy critical, complexity in manufacturing |
Manufacturing Processes: Magnetic Connector 2025
The manufacturing of magnetic connectors, a crucial component in various applications, demands precision and efficiency. Modern techniques are constantly evolving to meet the growing demand for higher performance and cost-effectiveness. This section delves into the specifics of manufacturing processes, focusing on automation, 3D printing, and sustainability considerations.
Common Manufacturing Techniques
Several established techniques are employed in magnetic connector production, each with its strengths and limitations. These processes include injection molding for plastic housings, machining for metal components, and specialized processes like wire winding for coil structures. The selection of the appropriate technique hinges on the specific connector design, material requirements, and desired production volume.
Automation and Optimization
Automation plays a pivotal role in streamlining magnetic connector production, enhancing efficiency and minimizing human error. Robotic arms are frequently integrated into assembly lines, enabling precise placement of components and improved throughput. Furthermore, advanced software tools optimize machine settings and predict potential issues, reducing downtime and improving overall production yield. Machine learning algorithms are being increasingly implemented to analyze data from the manufacturing process, leading to further improvements in quality and efficiency.
3D Printing Applications
D printing, particularly additive manufacturing, offers significant potential for creating complex geometries in magnetic connector designs. This technique allows for the fabrication of intricate internal structures within the connector, optimizing magnetic flux paths and potentially reducing material usage. Early adoption of 3D printing in prototyping stages of magnetic connector design has shown to expedite the design-to-production cycle and facilitate innovation in connector shapes and functionalities.
However, 3D printing currently faces limitations in the scale of production and the cost per unit for mass production, and materials with the necessary magnetic properties.
Sustainability Considerations
Sustainability is becoming a key driver in manufacturing decisions. Companies are exploring ways to minimize environmental impact throughout the lifecycle of magnetic connectors. This includes the selection of eco-friendly materials, reduction of energy consumption during production, and efficient waste management practices. Examples include using recycled plastics, adopting closed-loop systems for material recovery, and implementing energy-efficient machinery. The rising cost of raw materials and growing pressure from environmental regulations are driving this trend.
Challenges in Scaling Up Production
Scaling up magnetic connector production presents several challenges. Meeting the increasing demand while maintaining quality standards and cost-effectiveness is a significant hurdle. The complexity of the connector designs, coupled with the precision requirements for magnetic interactions, can make achieving high-volume production challenging. Further issues include supply chain disruptions and ensuring a consistent quality of raw materials.
Typical Manufacturing Process Flowchart
Step | Description |
---|---|
1. Material Procurement | Raw materials (plastics, metals, magnets) are sourced and quality checked. |
2. Component Manufacturing | Individual components (housings, coils, magnets) are manufactured via machining, injection molding, or 3D printing. |
3. Assembly | Components are precisely assembled, ensuring correct alignment and magnetic interaction. |
4. Quality Control | Rigorous testing is performed to validate functionality, magnetic strength, and dimensional accuracy. |
5. Packaging and Shipping | Finished connectors are packaged and shipped to customers. |
Applications in Various Industries
Magnetic connectors, with their inherent advantages in terms of speed, security, and design flexibility, are finding diverse applications across various sectors. Their ability to reliably connect and disconnect components rapidly, coupled with their compact size, makes them suitable for integration into a wide range of products and systems. This versatility opens doors to enhanced efficiency and innovation in diverse industries.
Applications in Consumer Electronics
Magnetic connectors are increasingly prevalent in consumer electronics, particularly in portable devices. Their ease of connection and disconnection facilitates user-friendly designs, allowing for quick battery replacements, accessory attachments, and seamless device integration. Examples include laptops with magnetic charging docks, smartphones with magnetically attached accessories, and headphones with magnetic earcups. This integration results in streamlined user experiences and increased device functionality.
Applications in the Automotive Industry
The automotive sector is leveraging magnetic connectors for various applications, including wiring harnesses, sensors, and even in-cabin accessories. Their robustness and ability to withstand vibrations make them ideal for the harsh conditions of automotive environments. This is particularly beneficial for electric vehicle (EV) development, where quick and secure connections are crucial for battery management and charging systems. Furthermore, magnetic connectors offer the potential for simplified assembly and maintenance processes in vehicles, leading to cost savings and increased efficiency.
Applications in Industrial Automation
In industrial automation, magnetic connectors facilitate the rapid connection and disconnection of machinery components. Their ability to handle high-current applications and withstand harsh industrial environments makes them a robust solution for diverse automated systems. Examples include robotic arms, assembly lines, and material handling systems. The use of magnetic connectors in these systems can significantly improve productivity and reduce downtime.
Applications in Aerospace and Defense
The aerospace and defense industries are increasingly considering magnetic connectors due to their reliability and ability to withstand extreme conditions. Their lightweight nature and compact design make them suitable for applications requiring minimal space and high performance. For example, these connectors could be integrated into aircraft wiring systems or defense equipment, enhancing the overall system reliability and minimizing weight.
Emerging Applications in Other Sectors
Beyond the sectors mentioned above, magnetic connectors are poised for significant growth in other sectors. Their adaptability and versatility suggest potential in medical devices, where their ability to connect and disconnect components could improve surgical procedures and patient care. In the construction industry, magnetic connectors might be used for temporary or permanent connections of structural elements, offering a rapid and efficient assembly process.
Additionally, in the agricultural sector, magnetic connectors could streamline equipment maintenance and repairs.
Summary Table of Applications
Industry | Application | Benefits |
---|---|---|
Consumer Electronics | Battery replacements, accessory attachments, device integration | User-friendly designs, quick connections, enhanced functionality |
Automotive | Wiring harnesses, sensors, in-cabin accessories, EV systems | Robustness, vibration resistance, simplified assembly, increased efficiency |
Industrial Automation | Robotic arms, assembly lines, material handling | High-current handling, harsh environment resistance, improved productivity |
Aerospace & Defense | Aircraft wiring systems, defense equipment | Reliability, extreme condition tolerance, lightweight design |
Emerging Sectors (Medical, Construction, Agriculture) | Medical device connections, structural connections, equipment maintenance | Improved surgical procedures, rapid assembly, streamlined maintenance |
Standards and Regulations
Magnetic connectors, crucial components in diverse industries, necessitate adherence to stringent standards and regulations. These ensure safety, interoperability, and maintain performance across various applications. Compliance with these standards is paramount for market access and sustained growth.
Relevant Industry Standards and Regulations
Standards for magnetic connectors encompass various aspects, including electrical safety, mechanical performance, and environmental compatibility. These standards are established by international and national organizations, ensuring a consistent level of quality and safety. Failure to comply can lead to product recalls, safety hazards, and legal ramifications.
Impact of Safety Standards on Connector Design
Safety standards directly influence the design of magnetic connectors. For instance, stringent requirements for insulation, material selection, and creepage distances are essential to prevent electrical hazards. The design must also consider potential mechanical stresses and ensure the connector can withstand expected loads and vibrations without compromising safety. These considerations are vital for preventing failures and maintaining reliable operation in diverse applications.
Compliance Requirements for 2025
Anticipating the evolving technological landscape and regulatory trends in 2025, magnetic connector manufacturers must proactively assess and address upcoming compliance requirements. Emerging standards focusing on sustainability, electromagnetic compatibility (EMC), and enhanced safety features will likely be prominent. Companies should proactively engage with regulatory bodies and industry associations to stay informed of the latest standards and their implications.
List of Relevant Regulatory Bodies and Their Guidelines
Numerous regulatory bodies play a crucial role in defining and enforcing standards for magnetic connectors. These include, but are not limited to, the International Electrotechnical Commission (IEC), Underwriters Laboratories (UL), and various national standards organizations. Their guidelines Artikel specific requirements for connector design, testing, and documentation.
How Certifications Affect Market Penetration
Certifications serve as a powerful tool for increasing market penetration for magnetic connectors. Demonstrating compliance with recognized standards builds trust and credibility with customers, potentially opening doors to new markets and opportunities. Certifications often provide a competitive edge in a global marketplace.
Summary Table of Key Standards, Compliance Requirements, and Benefits
Standard | Compliance Requirements | Benefits |
---|---|---|
IEC 60512 (Electrical Safety) | Meeting specific insulation standards, creepage distances, and test procedures. | Ensures electrical safety and reduces risk of electric shock. Demonstrates product reliability and enhances customer confidence. |
UL 224 (Mechanical and Environmental Standards) | Demonstrating the connector’s ability to withstand mechanical stresses, environmental conditions, and relevant test parameters. | Ensures the connector’s durability and reliability under different operating conditions. Boosts customer trust and reduces the risk of product failure. |
ISO 16750 (Magnetic Materials) | Compliance with specifications regarding magnetic properties, such as coercivity, permeability, and residual induction, to ensure optimal performance. | Ensures magnetic performance is within acceptable tolerances and enhances the reliability and accuracy of the connector in various applications. |
RoHS (Restriction of Hazardous Substances) | Avoiding the use of hazardous materials in the connector’s manufacturing process. | Promotes environmental sustainability and aligns with global initiatives to reduce harmful substances in products. |
Future Trends
The magnetic connector market is poised for significant evolution in the coming years. Emerging technologies like artificial intelligence and the Internet of Things (IoT) are expected to reshape the design, manufacturing, and application landscape of these crucial components. Understanding these trends is critical for staying ahead of the curve and capitalizing on the opportunities they present.
Impact of Artificial Intelligence and Machine Learning
AI and machine learning (ML) are poised to revolutionize magnetic connector design optimization. Algorithms can analyze vast datasets of material properties, manufacturing processes, and performance data to identify optimal designs for specific applications. This leads to more efficient connector geometries, minimizing material usage and maximizing performance. Furthermore, AI-powered predictive maintenance can forecast potential failures, enabling proactive maintenance strategies and reducing downtime in critical applications.
Examples of this include the use of AI in the automotive industry to optimize the design of engine components and the use of ML in the aerospace industry to improve the reliability of aircraft systems.
Impact of Renewable Energy Technologies
The growing demand for renewable energy technologies, including wind turbines and solar panels, presents new challenges and opportunities for magnetic connectors. These applications often require robust, high-performance connectors capable of withstanding harsh environmental conditions and fluctuating power loads. The future of magnetic connectors in renewable energy will likely involve advancements in materials science, enabling connectors to withstand extreme temperatures and corrosive environments.
Increased demand for these specialized connectors is expected to drive innovation in the market.
Role of IoT and Interconnected Systems
The integration of magnetic connectors into interconnected systems via the IoT will enhance the monitoring and control of various applications. Real-time data acquisition from these connectors can facilitate predictive maintenance, optimize energy consumption, and enhance overall system efficiency. For example, smart grids can use IoT-enabled magnetic connectors to monitor power flow and identify potential faults in real time.
This data can be used to optimize energy distribution and prevent outages.
Future Materials and Technologies
Advancements in materials science will play a crucial role in shaping the future of magnetic connectors. New alloys with enhanced magnetic properties, improved corrosion resistance, and enhanced thermal stability are likely to emerge. These advancements will allow for the development of smaller, more powerful connectors with improved reliability. Furthermore, the use of composite materials may offer a balance between strength, weight, and cost-effectiveness.
Potential Market Disruptions
Several factors could potentially disrupt the magnetic connector market. The rise of new, more efficient power transmission technologies, or the adoption of alternative materials with superior properties could potentially alter the current market share. Furthermore, changes in consumer preferences and technological advancements in other fields can also cause unexpected shifts in demand. The increasing emphasis on sustainability and environmental considerations may lead to regulations that influence the choice of materials and manufacturing processes.
Potential Future Trends
- Increased use of AI and ML for connector design optimization.
- Growing demand for specialized connectors in renewable energy applications.
- Integration of IoT for enhanced monitoring and control of interconnected systems.
- Development of new materials with enhanced magnetic properties, corrosion resistance, and thermal stability.
- Emergence of alternative power transmission technologies potentially impacting the demand for magnetic connectors.
- Potential regulations focused on sustainability and environmentally friendly materials.
Cost Analysis
Magnetic connectors, while promising advancements in various sectors, must be assessed for their cost-effectiveness against traditional connectors. A comprehensive analysis considers material costs, manufacturing processes, and long-term implications. The financial viability of this technology hinges on its ability to justify the investment compared to existing solutions.
Cost-Effectiveness Compared to Traditional Connectors
The economic viability of magnetic connectors hinges on a comparison with traditional methods. Traditional connectors often rely on mechanical fasteners or soldering, offering established manufacturing processes. However, magnetic connectors may offer advantages in terms of assembly speed and reduced material use, potentially offsetting higher initial material costs. Analysis must consider these contrasting aspects to determine overall cost-effectiveness.
Material Costs
The cost of materials significantly influences the overall price of magnetic connectors. Rare earth magnets, often crucial components, exhibit fluctuating prices based on global market conditions and supply chain factors. The price of other materials, such as conductive polymers or shielding metals, also plays a role. Factors such as the volume of production and the specific material grades chosen directly impact the final material cost.
Manufacturing Costs
Manufacturing costs associated with magnetic connectors vary based on design complexity and production volume. Automated assembly lines may lower costs for high-volume production. However, the specialized equipment required for certain manufacturing stages might increase the initial investment. These manufacturing processes are subject to change based on technological advancements and production scales.
Long-Term Cost Implications
The long-term cost implications extend beyond initial purchase price. Factors such as maintenance, repair, and potential for obsolescence must be considered. Magnetic connectors, due to their unique design, may require specialized maintenance or replacement procedures. This aspect needs to be thoroughly assessed to determine the overall cost-effectiveness over the lifespan of the product.
Cost Variations
Cost variations across different magnetic connector designs stem from several factors. The type of magnet, the connector’s geometry, and the required shielding significantly affect costs. For instance, high-performance magnets with greater magnetic strength often come with a premium. Similarly, more intricate designs for specialized applications usually involve higher manufacturing costs.
Comparison of Different Connector Designs
Different connector designs have distinct cost implications. A simple, low-performance design will typically be cheaper than a high-performance, complex design. A comparison should consider the desired magnetic force, the operating environment, and the required lifespan of the connector. Detailed cost analysis of each design is necessary for informed decision-making.
Cost, Benefits, and Value Propositions
Cost Factor | Benefits | Overall Value Proposition |
---|---|---|
Material Costs (Rare Earth Magnets) | High Magnetic Force, Compact Design | Cost-effective for applications requiring high force or space efficiency |
Manufacturing Complexity | Speed of Assembly, Reduced Parts | Potential cost savings in assembly time and inventory |
Long-Term Maintenance | Durability, Reliability | Long-term cost savings through reduced failures and replacements |
Design Complexity | Specialized Applications, High Performance | Cost-effective for specific needs requiring enhanced performance |
Supply Chain Considerations
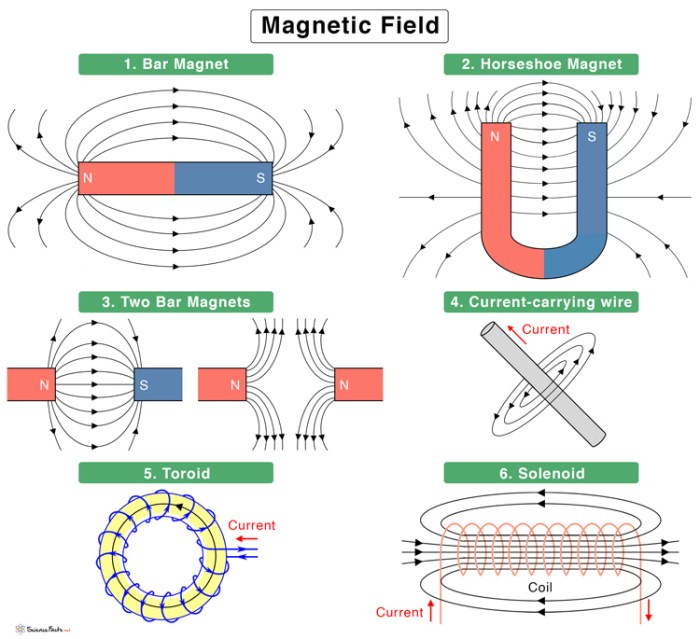
The global supply chain for magnetic connectors is complex, involving numerous suppliers, manufacturers, and distributors across various geographical regions. Understanding this intricate network is crucial for anticipating potential disruptions and developing robust mitigation strategies. This section delves into the key aspects of the magnetic connector supply chain, including potential risks, alternative sourcing options, and geopolitical factors.
Global Supply Chain Analysis
The global supply chain for magnetic connectors is characterized by a geographically dispersed network. Key components, such as raw materials (rare earth elements, copper, polymers), manufacturing facilities, and assembly operations, are often located in different countries. This dispersion, while allowing for cost optimization, also introduces vulnerabilities to disruptions. Analysis of the supply chain involves identifying the key players, their geographical locations, and the flow of materials and finished products.
Potential Supply Chain Risks and Vulnerabilities
Several factors can disrupt the magnetic connector supply chain. Geopolitical instability, natural disasters, pandemics, and economic downturns are all potential risks. Furthermore, supplier bankruptcies, raw material shortages, and transportation bottlenecks can significantly impact production and delivery timelines. These vulnerabilities highlight the need for diversification and contingency planning.
Strategies for Mitigating Risks
Implementing strategies to mitigate supply chain risks is crucial. Diversifying supplier bases across multiple countries reduces reliance on single sources. Establishing robust communication channels with suppliers helps in proactive risk management and early warning systems. Developing contingency plans for potential disruptions, such as alternative sourcing options and backup logistics routes, are essential for maintaining operational continuity. Building strategic partnerships with suppliers that offer complementary capabilities can enhance resilience.
Alternative Sourcing Options
Exploring alternative sourcing options is vital for mitigating risks associated with dependence on a single supplier. This could involve identifying and vetting new suppliers in different geographical regions. This can enhance resilience by reducing vulnerability to disruptions in one region. A critical factor is the quality and reliability of alternative suppliers, ensuring that their production capabilities and quality control meet the required standards.
Geopolitical Factors
Geopolitical factors can significantly impact the magnetic connector supply chain. Trade wars, tariffs, sanctions, and political instability in certain regions can disrupt the flow of materials and finished goods. These factors need to be carefully assessed, and strategies must be in place to adapt to fluctuating geopolitical conditions. For example, the recent trade disputes between major economies have created uncertainty in the global supply chain.
Supply Chain Diagram, Magnetic connector 2025
This visual representation depicts the flow of materials and products from raw material extraction to the final delivery of magnetic connectors. The diagram highlights the various stages, suppliers, and potential points of disruption.
Summary
In conclusion, magnetic connectors are poised for significant growth in 2025, driven by innovations in design, manufacturing, and applications. This report offers a comprehensive analysis of the market landscape, outlining potential opportunities and challenges. The future of magnetic connectors appears promising, with continued advancements and a diverse range of applications.
Detailed FAQs
What are the key market segments for magnetic connectors in 2025?
Key segments include consumer electronics, automotive, industrial automation, aerospace, and defense. Further breakdowns of these segments may be found in the detailed market overview section.
What are the projected growth trends for magnetic connectors in 2025?
Projected growth is significant, with factors like miniaturization, improved performance, and cost-effectiveness driving market expansion across multiple sectors.
What are the potential supply chain risks for magnetic connectors in 2025?
Potential supply chain risks include geopolitical factors, material shortages, and manufacturing disruptions. The report discusses strategies for mitigating these risks.
How do safety standards impact the design of magnetic connectors in 2025?
Safety standards play a crucial role in connector design. Compliance with relevant regulations is vital for market penetration and product safety.